Automated labeling equipment is versatile. There are many different ways that this technology can apply to your production needs. Equipment types vary based on your products and the level of automation required, but Summit's team of technicians and engineers are available to assess your operation, and create a plan for your business.
Methods for Applying Labels
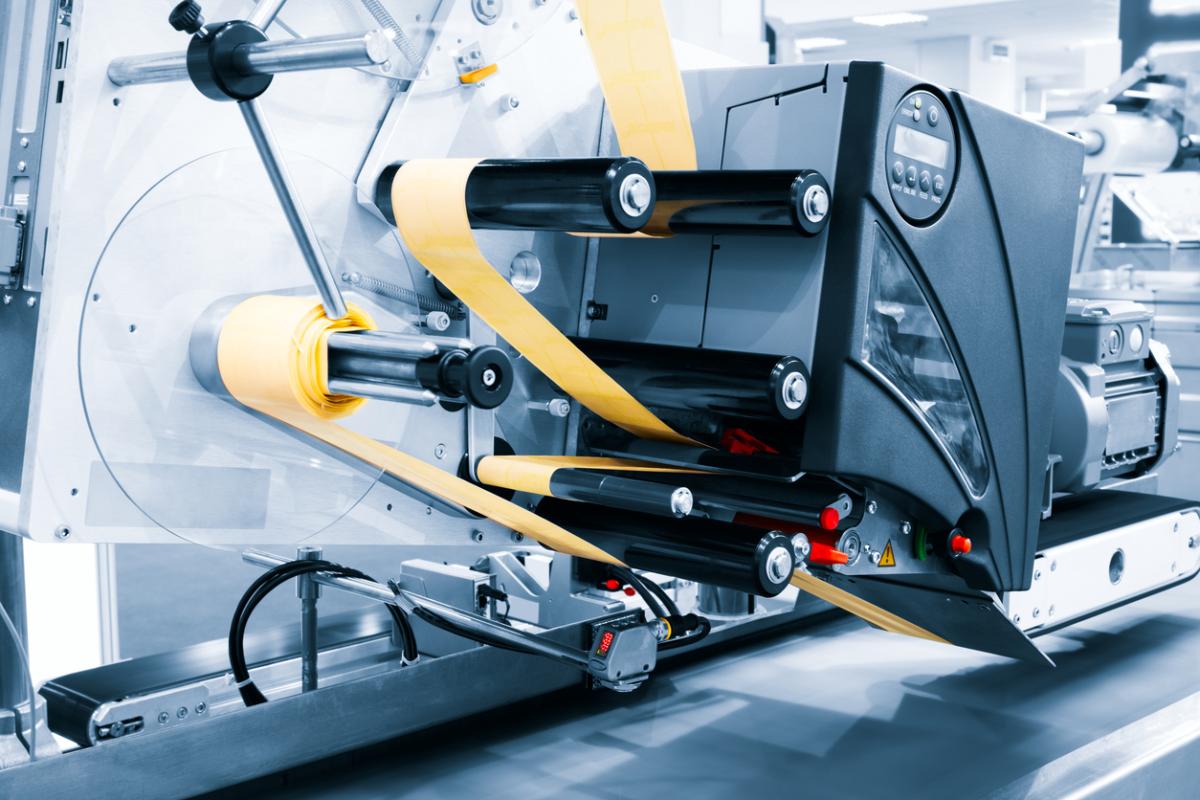
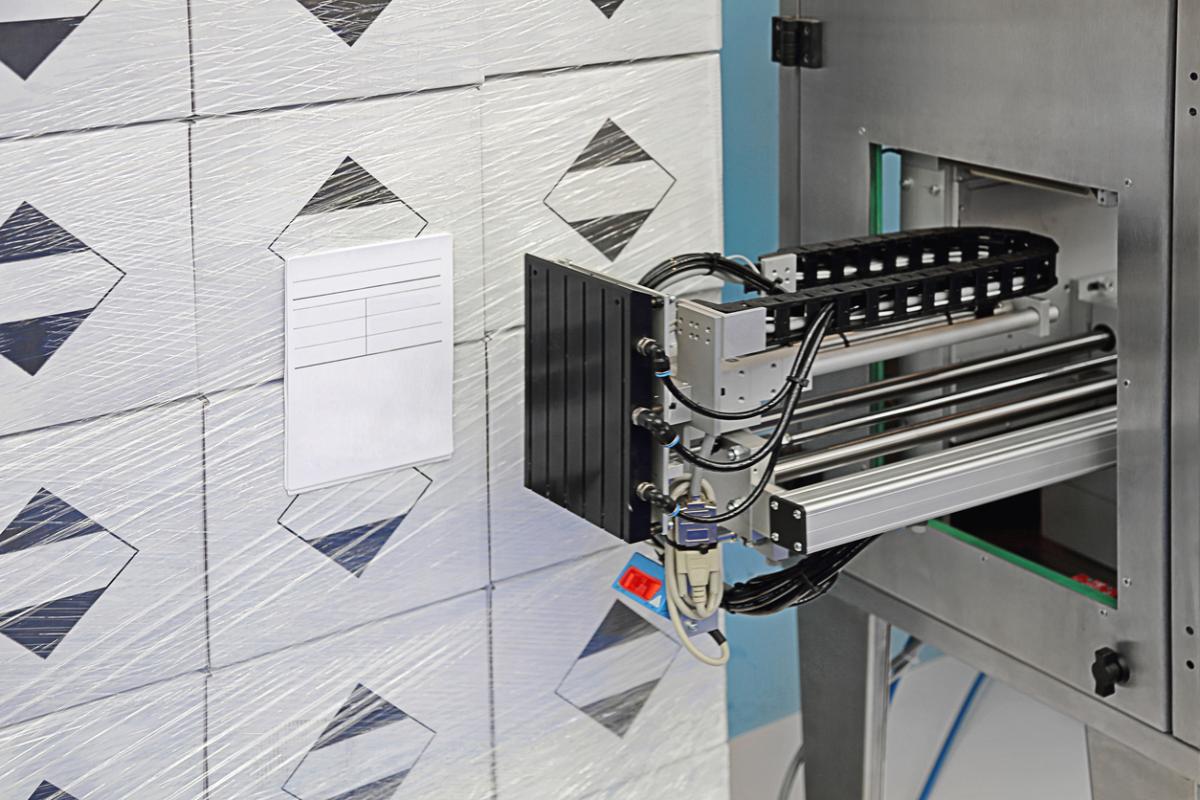
Some of the most common methods for label applications are:
- Merge applicator (also known as wipe-on): guiding products past a stationary label dispenser, which then applies pressure to adhere labels onto the surface of the product as it moves along the conveyor belt. This method is commonly used for curved surfaces like bottles or canisters. The “wipe-on” method can be compatible with any angle of the product.
- Air-blow: compressed air to precisely blow labels onto products, ensuring accurate placement without physical contact between the label and the product surface. This method is very versatile and adaptable – if different products require different label placement, the equipment can be quickly adjusted to accommodate. Depending on your production set-up, the air-blow label application method can be faster than other approaches.
- Tamp: pneumatic or mechanical arm to pick up labels and then press them onto products with controlled force and accuracy, commonly used for flat surfaces. The tamp method for applying labels has some similarities to the air-blow method – it also utilizes pressurized air to affix a label. The automation equipment utilized with the tamp method requires size-specific pads that correspond to a specific label.
Types of label applicators offered by Summit
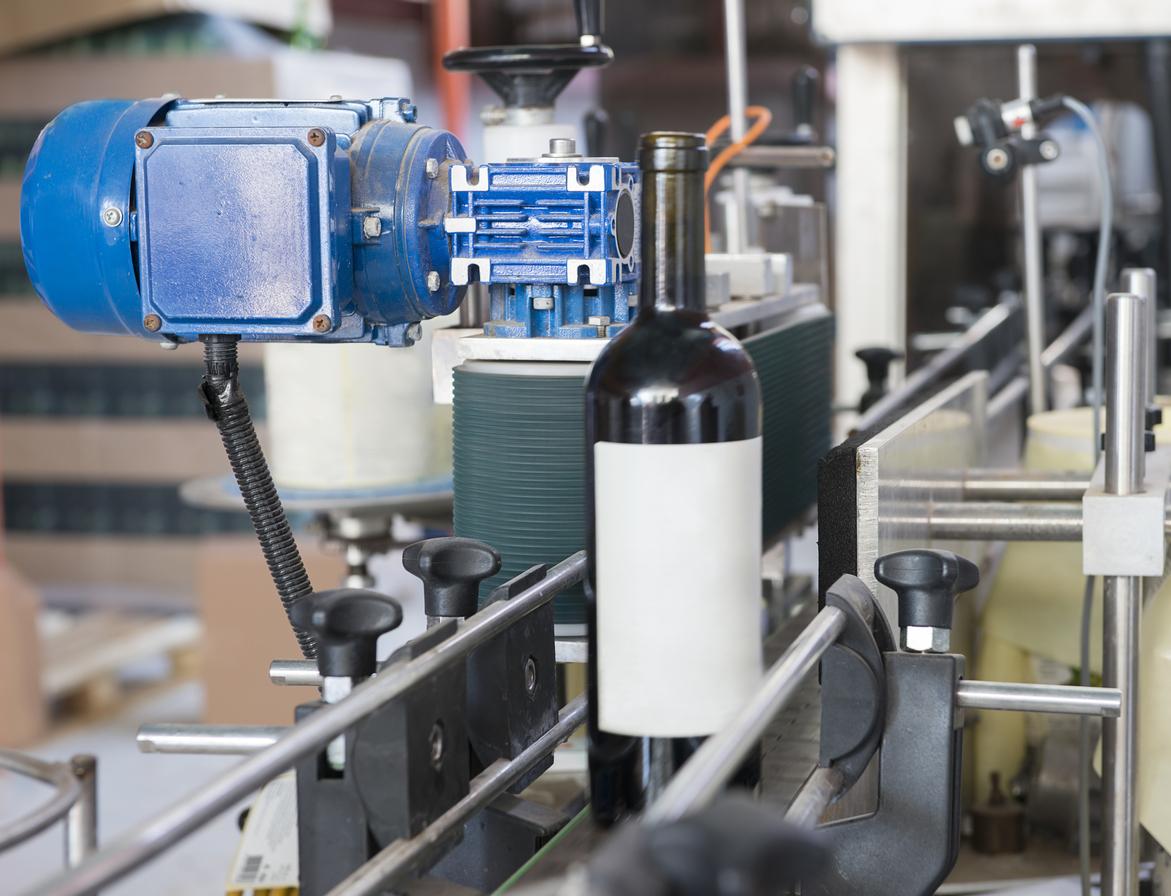
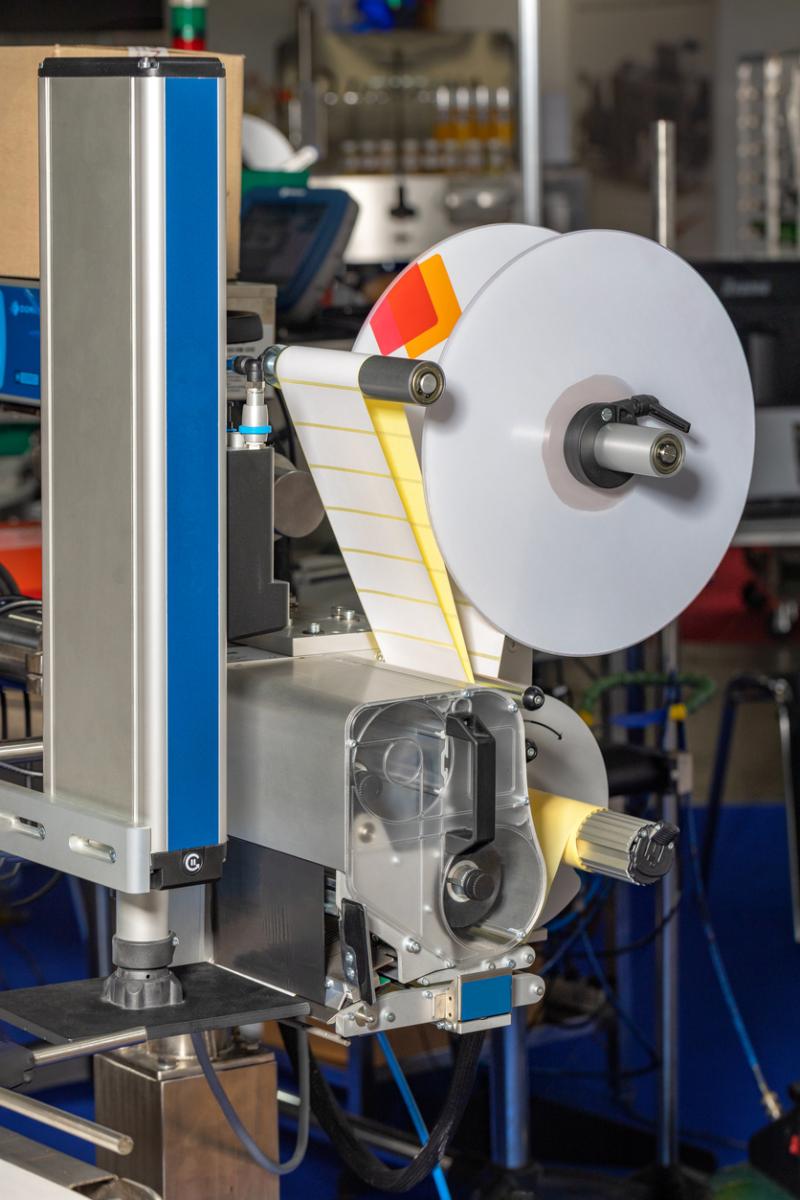
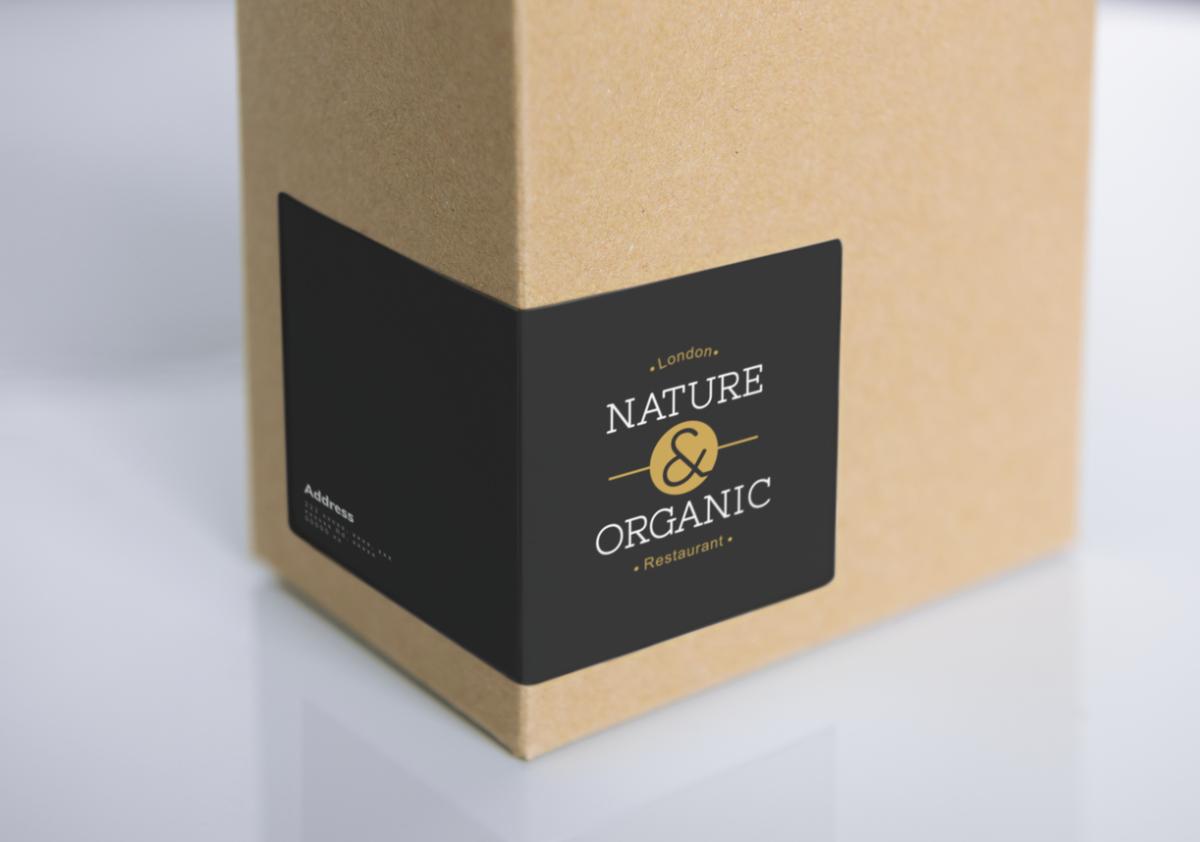
- Pressure-sensitive label applicator: These machines apply labels by pressing adhesive-backed labels onto products. They're versatile and can handle various product shapes and sizes, making them suitable for bottles, pouches, boxes, cartons, and pallets.
- Wrap-around labeler: Specifically designed for cylindrical containers like bottles or cans, these machines apply labels by wrapping them around the product. They ensure consistent alignment and placement of labels, commonly used in beverage and food industries.
- Print and apply labeler: These machines not only apply labels but also print variable information such as barcodes, serial numbers, or expiration dates on labels in real time. They're versatile and commonly used in industries requiring on-demand labeling and traceability.
- C-wrap labeler: A specialized type of label applicator designed for applying labels onto the leading edge of a product, wrapping around one side (leading edge) and slightly onto the adjacent side. This creates a "C" shape around the product. C-wrap labelers are commonly used for products such as bottles, jars, or containers where a front-facing label with partial coverage on the top is desired. They ensure consistent label placement and can accommodate products of varying shapes and sizes. C-wrap labeling is popular in industries such as food, beverage, and personal care for branding and product identification purposes.
- Front and back labeler: Ideal for products requiring labels on both the front and back, these machines apply labels to two sides of a product simultaneously. They're commonly used for bottles, jars, and containers in the pharmaceutical, food, and cosmetic industries.
- Top & Bottom labeler: These machines apply labels onto the top surface of products such as pouches, boxes, or cartons. They ensure precise placement and are often used in packaging applications where branding or product information needs to be prominently displayed.
- Pallet labeler: Designed for large-scale applications, these machines apply labels to pallets for inventory tracking, shipping, and warehouse management purposes. They ensure accurate placement and adherence of labels on pallets.
- Tamper-evident labeler: These machines apply labels designed to break or show signs of tampering upon opening, ensuring product integrity and safety. They're commonly used in pharmaceuticals, food, and beverage industries to prevent product tampering and counterfeiting.
Application Factors to Consider
- Communications with Internal Systems (most used for Print and Apply printers): The Programmable Logic Controller (PLC) manages both the printer and applicator while interfacing with your operating technology system. It stores label printing formats and generates text and barcodes according to data received from the OT system. Due to the unique nature of each production environment, various options exist for print engines, applicators, and PLC interfaces. Understanding how these components integrate enables machines to meet diverse requirements through tailored design choices.
- What level of automation do you need? Depending on your throughput needs (products labeled per minute) and the amount of labor you have at your disposal, there are manual, semi-automatic, and automatic labels designed to fit your production level.
- Do you have the right labels for this machine?
- Do the labels need to come on a roll or in a fan-folded stack?
- If on a roll, is it the correct core size (1” and 3” are most common) and do the outer dimensions (OD) of the roll fit within the housing of the machine?
- What is the label's orientation (vertical or horizontal) and what is the wind direction (inside or outside)?
- What material is the label made from (paper, film, other), and what adhesive type is used (adhesive type (permanent, removable, freezer-grade, etc.)? Also, is there any coating on the label (matte, gloss, thermal transfer, etc.)?
- Backing paper: what type of material is the backing paper substrate? How far apart are the labels from one another? Are the perforations on the backing paper between labels?
- Label Size and Shape: Ensure that the label applicator can accommodate the size and shape of your labels without causing jams or misalignment during the application process.