You've probably read the headlines about labor shortages. Companies worldwide are having trouble finding workers to fill positions. This is causing problems for businesses across the globe and especially in the US. In this article, we will look at the causes of worker shortages and how they affect our supply chain.
Supply chains have become a critical part of business operations in recent years. As more products move from manufacturer to retailer or wholesaler to consumer, it becomes increasingly important that these processes run smoothly. In a previous article, we detailed the cost of plastics, the causes of the current shipping delays, and the breakdown in the global supply chain.
Worker shortages directly impact shipping and cause massive supply chain issues. The global pandemic has crippled the supply chain by making it unsafe for workers to return to offices, forcing worker relocations from cities to suburban and rural areas, and opening the possibility of career changes during lockdowns.
COVID-19 scares cause worker shortage
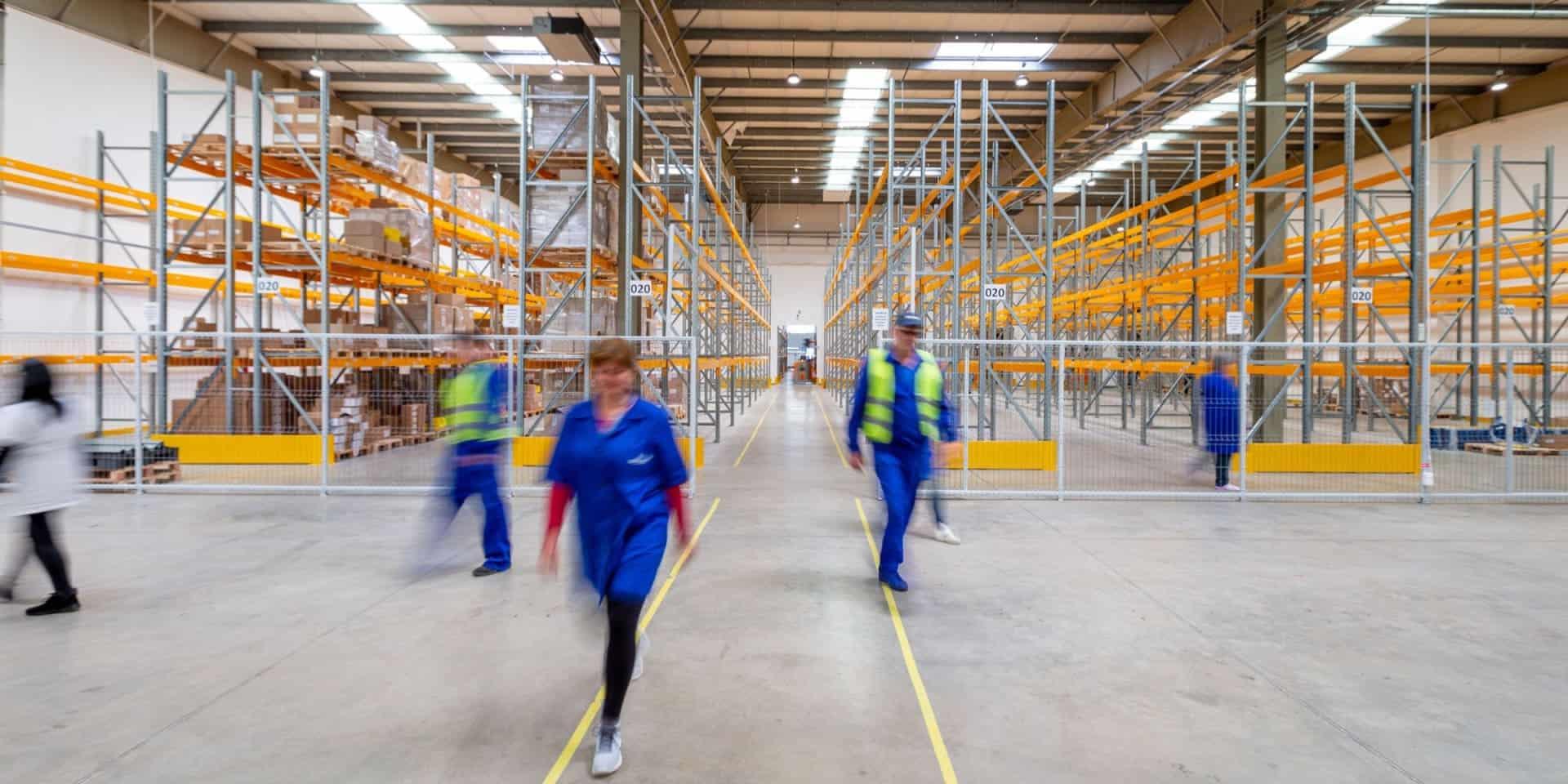
Imagine if you were certain that if you went to work, you would not make it home safe–maybe not even alive. Whatever you think about the coronavirus, that basic fear has been the experience of hundreds of thousands of workers over the past 18 months of the COVID-19 pandemic.
As the virus spread throughout the country, many employees who had never before considered leaving their jobs decided to do so. Others found themselves unable to find new employment after being laid off during the economic downturn. And some simply stayed home because they didn't want to risk getting sick.
Job hunting and hiring during a Pandemic is not the same as it was in the past. An in-person job could take a parent away from their child, and it could also bring increased risk of infection. Remote jobs, while growing as a percentage of the workforce, are not always possible.
The other problem for workers is a skills mismatch. Workers looking for jobs aren't finding quality work. A survey by FlexJobs showed that while 69% of workers were actively looking for work, 46% of those workers only found low-wage job openings. However, 40% said they would take lower paid work if they could get it.
Labor shortage in US driven by location mismatch
Some of the labor shortage in the US is due to simple geographic distance. As the pandemic required governments to shutdown businesses across the country, many hourly and low-wage workers were left with either no income or reduced incomes from unemployment.
In order to save money, a large portion of these workers moved to less expensive parts of the country or back home to stay with family. Now, with the economy finally starting to see some life, these same workers are trying to move where the good jobs are.
But that takes time.
According to the Society of Human Resource Management, we don't have a labor shortage. There are 9.5 million unemployed people and those looking for work, but there are 9.2 million job openings. And according to the Bureau of Labor Statistics, June saw the number of people looking for jobs grow.
The answer could simply be that the people looking for jobs aren't near the right jobs for their skills anymore. Despite the rise in remote work, most jobs (including service jobs, manufacturing jobs, and retail jobs) cannot be done remotely. For most jobs, proximity matters. If you aren't nearby, you can't get the job.
Workers choosing career changes causing a shortage
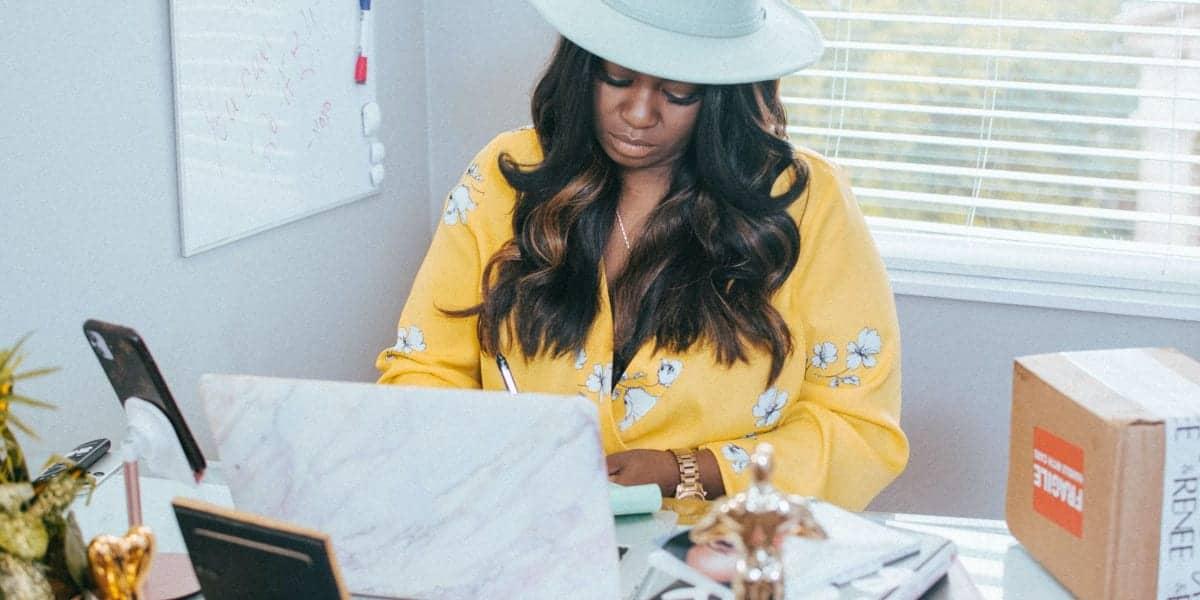
The pandemic caused many workers to think differently about their careers. Or lack thereof.
From May through July 2021, LinkedIn reported that about 57 percent of its job switch activity was between different industries. These massive shifts from one industry to another are causing production to lag as new workers transition to new careers. It takes time to retrain.
Not only are workers opting into different careers, some are using this opportunity to start their own businesses. In fact, through September, Americans filed a record 1.4 million business startup applications, according to an analysis of Census Bureau data by EIG. Most of these startups are in industries like manufacturing or retail where they're likely to create new jobs, rather than freelance workers who rarely create jobs. That could be a positive sign for the future, but it does little to help the economy now.
Is the labor shortage due to unemployment benefits?
What about those enhanced unemployment benefits? A majority of business owners think that the expanded COVID-19 unemployment benefits are the main reason that it's hard to find workers. This line of thinking has prompted a majority of states to curtail or stop additional payments to unemployed workers, in order to incentivize them to return to the workforce. It makes a certain type of intuitive sense: if you stop giving people free money through expanded unemployment benefits, they will have to return to work in order to make a living.
But that hasn't been the case.
In the 26 states that opted to end at least one pandemic unemployment program, not one of those states saw employment growth in the months after. This is in line with several studies that have found that the enhanced federal unemployment benefits have only had a minor effect on whether workers look for a job or accept an offer of employment.
In short, according to research conducted by economists from Harvard University and Columbia University, cutting off unemployment insurance for some people who lose their job could cause hundreds of thousands of new hires in early fall. This may cost millions of dollars in lost government revenue due to fewer consumers buying goods and services. It would slow down job creation and hiring, which is in line with what we are seeing now.
Effects of labor shortage on the packaging industry

We have already written about how the supply chain disruptions, in part due to labor shortages, have drastically increased costs for packaging materials and equipment.
From the packaging industry’s perspective, one positive outcome from this labor shortage, has been the innovation and widespread adoption of automated and robotic technology in packaging operations.
Packaging and labeling companies like ours are increasingly helping businesses solve their packaging issues – and their labor shortages – with high-tech solutions to improve efficiency and streamline operations. This switch is not without its growing pains, as you can't simply order a few machines and be fully automated. It takes time to adjust the manufacturing processes and personnel to take advantage of new efficiencies.
Unfortunately, the delivery of these machines also takes more time right now due to the same shipping delays, supply chain disruptions, and worker shortages we’ve been discussing. It also takes time to get a return on the capital invested in new equipment. Our typical ROI sees our customers get a return on their investment in about 12 months. This is down from 3 years, which was the industry standard for years. Even though packaging automation takes time and resources to deploy, we’re seeing healthy demand for this type of equipment spurred on in part by the realities of the pandemic.
While our packaging equipment lines range from semi-automated to fully automated, we don’t pigeonhole our customers into the most expensive solution. We work with each client individually to understand their specific goals and needs. In an era of labor shortages, we often end up recommending state-of-the-art robotic or automated packaging equipment solutions to help our customers operate more efficiently and productively, especially during times when navigating staffing shortages. But this solution isn’t assumed when we go into a company to spec out the right piece or pieces of equipment.
The type of equipment chosen often has an impact on the company’s head count going forward. However, in our experience, the final decision on the type equipment purchased isn’t a purely capitalistic decision for customers. Yes, it has to make financial sense, but for many of our customers, they have been dealing with labor shortages for years, shortages that have been heightened all the more by the pandemic. In these cases, leaning harder toward automation is simply reading the writing on the wall.
In a 2018 interview we did with Shane Dittrich, CEO of House of Design, he discussed the problem of finding enough skilled labor:
"The problem right now in the U.S. is not that we’re losing jobs. The challenge is finding people to fill the jobs. Every manufacturer I talk with complains about not having enough people. Will robots replace tasks that humans are now doing? Yes, but that person is typically moved into a more value-add position. We provide the machinery, infrastructure, and robots to help companies afford to onshore their manufacturing processes permanently. We are helping to change jobs that are unsafe, unfulfilling, and have high turn-over rates into jobs that are more engaging and have a higher skill set that becomes marketable for the individual. The demand for automation is changing jobs and when companies have great employees, they invest in them to learn new skills within the company."
And that was before the coronavirus pandemic changed much of what we understand about the labor market.
As we move forward, we see businesses investing even more in automation and hiring more skilled labor to run (and maintain) these machines. As always, Summit will be right there to help with packaging solutions, materials, and equipment automation.