The current global shipping crisis and delays have caused many operations and purchasing managers to scream into their phones, “How long will it take to get my order?” No matter how much they want, or need their goods, relief isn’t close by.
As a packaging materials supplier, we’re doing more than ever to communicate with our customers about their orders, their timelines, and their cost of goods.
We’ve written some articles on the rising cost of packaging materials and the slowdowns in the global packaging supply chain. We thought it would be helpful for this article to zoom out a little from our industry and focus on what’s going on globally with shipping.
As the world becomes more connected through technology, the supply chain has grown more complex and fragile. This means that the time between when products are manufactured and when they reach consumers is getting longer than ever. Throw in a worldwide pandemic, seasonal storms, and a shortage of shipping containers, and you have a recipe for real disruption.
In this article, we will look at what causes these shipping delays, why they happen, and how they affect the global, and national, supply chain.
Why are there shipping delays?

The quick answer is COVID-19, but the accurate answer is much more complicated. Global and US shipping delays have created a logistical crisis that affects almost every industry. The pandemic has disrupted production of everything from medical equipment to toilet paper, which then leads to further complications within each company’s own supply chains.
Shipping companies like UPS and FedEx have been working around the clock to keep up with demand for shipments across the globe. However, as you can imagine, things aren’t going well right now because of all the cancellations and changes orders.
COVID-19 pandemic is the primary culprit behind shipping delays
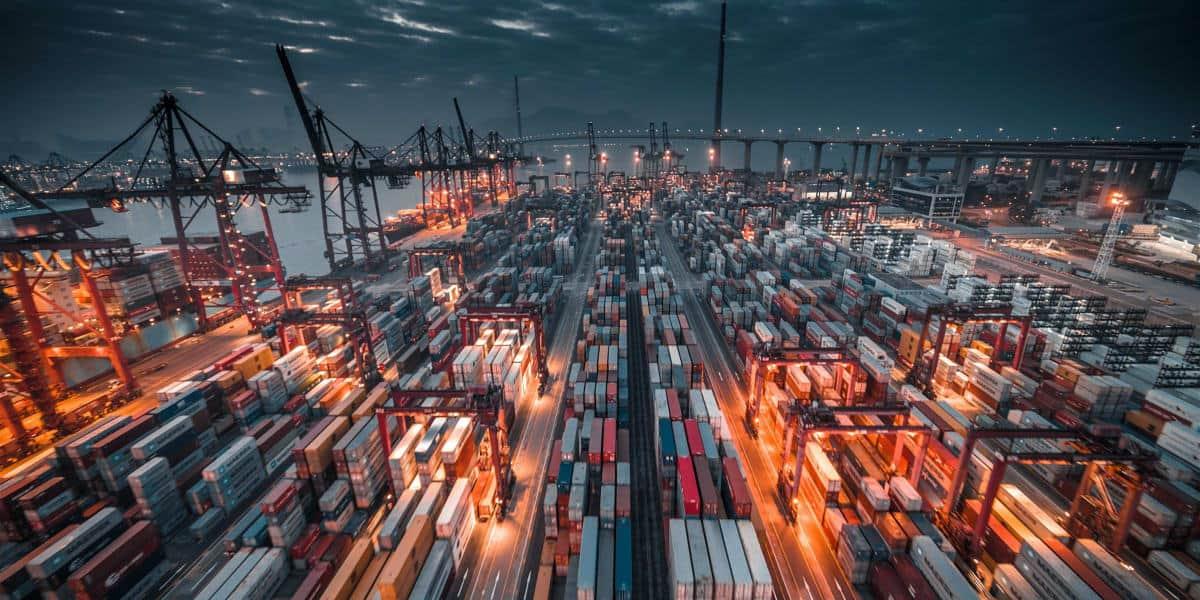
We would love to blame COVID-19 for the current shipping crisis, but that isn’t the entire picture. Our global supply chain was fragile even before coronavirus slammed into our economy like a battering ram. The pandemic only made what was already broken that much worse.
When a new virus emerges, some people get sick and others panic. Workers stop coming to work, either because they can’t or are afraid to, which slows down production lines in mines and factories around the globe. And as soon as production slows down, shipments of raw materials like plastics and metals get delayed.
This all adds up to one big problem: A shortage of supplies across industries. It also doesn’t help that some countries have been stockpiling resources because they fear shortages.
Global Supply Chain 101
How did it come to this? First, we need to understand how transportation issues affect the global economy. Let’s start with Econ 101; it’s cheaper to ship cargo across the water than over land. Our current global economy is built on that fundamental reality.
For the last century, western countries moved manufacturing to Asia and Latin America because the cost to produce overseas and ship to the US and Europe was cheaper than making products domestically.
But what happens when the math doesn’t work out? Our entire system is in jeopardy when shipping costs go up by exponential amounts because companies can’t afford to ship goods or wait until rates drop.
Our complete system of international trade assumes that goods shipped over water are cheaper than goods shipped over land. Now that shipping costs have risen worldwide, that system is in danger.
Ports Congested
Not only are shipping costs rising, but the goods that are shipped can’t reach their destinations on time. As COVID-19 ravages dock workers across the world, ports can’t unload the container ships already docked in their ports, much less handle the dozens of additional container ships waiting to offload their cargo. According to one source for a major North American ship operator, ports are operating at 60% capacity at best.
Inclement weather systems in the Pacific have only complicated an already dire situation, forcing ports without COVID-19 outbreaks to reroute ships away from them. But, as the list of available ports shrinks, ships stack up outside of the few functioning ports, and costs continue to rise.
Transportation over land limited
The same problems with the pandemic that affect ports are also wreaking havoc on overland shipping as well. The costs of transporting goods overland by semi-truck have risen as well. Truck drivers calling in sick or retiring early, warehouse workers finding new, less hazardous employment, and even key operations staff at trucking companies removing themselves from the workforce have contributed to a dire situation.
In fact, finding truck drivers has become so difficult that some firms are trying to import drivers from overseas.
Shipping delays in USA
While the USA isn’t immune to problems with the global shipping system, shipping delays in the US are particularly driven by clogged ports, complications from COVID-19, and rapidly increasing demand.
California ports slow
As dozens of container ships sit anchored off the coast of California, ports in Los Angeles and Long Beach are doing their best to process the ships that are lucky enough to make it into port. Those ships represent millions of shipping containers containing tens of millions of tons of goods that can’t make it to their destinations — retail stores, factories, warehouses, and ultimately consumers.
The goods on those ships will be stuck in the bay for weeks, if not months. That’s a huge problem for our national supply chain. When a factory can’t get the materials it needs, it can’t make the goods consumers want. And those millions of containers removed from circulation cause shortages of containers worldwide.
How COVID has affected US shipping
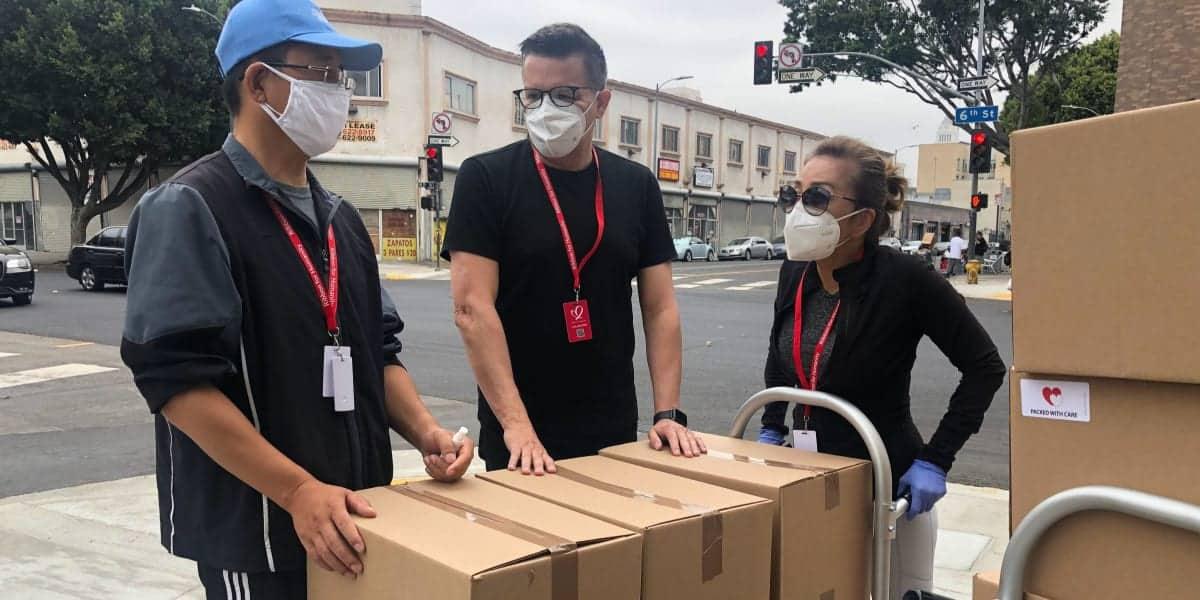
The biggest reason that ports in the US are slowing down can be summed up in one word: labor. There simply aren’t enough men and women to run the ports and move containers off the ships and onto trains and trucks. The main cause for labor shortages in the ports across North America and the US is undoubtably COVID-19. With laborers in the shipping industry either getting sick or worried about spreading the virus, the busiest shipping lanes can’t move the same amount of cargo they once used to.
Massive increases in online ordering
In addition to clogged ports and covid related worker shortages, Americans have never been more in love with ordering their merchandise to be delivered to their doors. The pandemic broke open this practice and now it’s almost expected to get next-day delivery of whatever you order on Amazon.
62% of consumers say that they shop more online now than before the pandemic. That drastic increase has led to more shipping, which has only increased costs.
Bonus reason: Diminished US Manufacturing Capacity
America’s capacity to manufacture almost everything has been decimated by offshoring, and even products made in the United States are likely to use raw materials or components that need to be imported for other reasons. Pharmaceutical manufacturing, for example, has been hampered by the fact that many active ingredients are imported from China or that only some drugs are manufactured overseas. Other commodities like steel and sheet metal used to build warehouses and factories are in short supply because of a tight labor market and companies that want to expand their capacity to manufacture or store more inventory are facing shortages of their own.
Examining global shipping delays
COVID has affected overseas shipping, especially Asian in countries. To stymie the spread of infections, countries from China to Vietnam and Malaysia have closed ports and decreased worker shifts. Now, 77% of global ports are experiencing some kind of delay or lengthened turnaround time.
Some global analysts are quick to blame the just-in-time manufacturing system, where the bare minimum of stock is maintained by manufacturers in their own factories to save on costs and space. This lack of reserves has caused a severe strain on one end of the supply chain, disrupting entire production cycles, and contributing to the global supply chain crisis. While we understand the value of JIT for our customers, we acknowledge that the model is being tested as never before.
Some industry experts are advocating more local just-in-time manufacturing and supply, shorting the supply chain, while getting the right materials to the businesses and consumers that desperately need them, a movement we’ll be watching with more than just curiosity.
So, why are shipping costs so high?
In short; it’s very complicated. The global supply chain is a complex system of thousands of interconnected parts, all working together to get you a package or shipment to your door or loading dock on time. When one, then two, then several more parts of that system break down, it becomes harder to ship the products and materials we purchase.
The lingering and devastating impacts of the global pandemic have simply shown the cracks in a fragile system. As port workers, truck drivers, and other logistical and support staff get sick with COVID-19, or the ports attempt to prevent the spread of the virus, ports inevitably close down or decrease their capacity. Slower loading and unloading at ports mean more backup at ports, which means fewer container ships delivering cargo.
And yet demand is only increasing. This increased demand on the part of consumers, in conjunction with diminished capacity for delivering the purchased goods, has skyrocketed shipping costs to 10 times their pre-pandemic costs.
As the holiday season approaches, critical relief is nowhere near, even as higher vaccine rates abate the coronavirus pandemic across North America.
What does this mean for the packaging industry?
It’s never been more important to have the right packaging supplier who understands the industry and can get you the right packaging materials when you need it. The cost of packaging is increasing faster than we’ve ever seen it, by more than 50% in some cases:
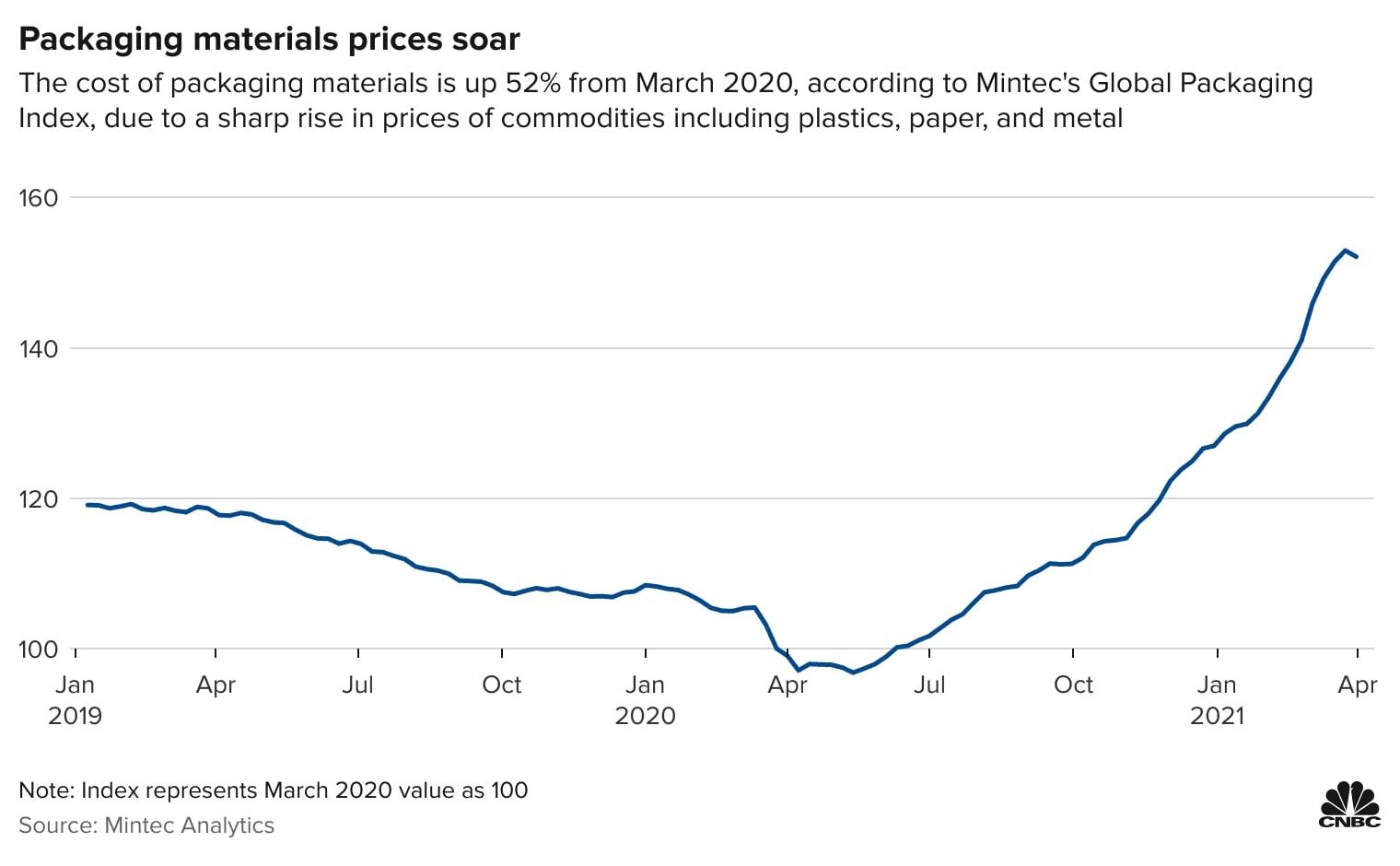
With costs increasing across the industry, the details matter more than ever. As things evolve regarding shipping and material costs and delivery times, we’re working hard to keep our customers up to speed on all aspects of their material ordering.
We’re also committed to looking at every possible way we can add value to our customer’s packaging departments.
Everyone at Summit Packaging understands that the pandemic has created labor shortages that effect their operations too. We believe that packaging suppliers like us, who offer full service to their customers, from materials to equipment and even technical expertise, are in the best position to help customers rebound from the challenges of the pandemic.
We can’t always shelter our customers from rising costs, but we will do everything we can to get creative with their packaging solutions to keep them on their feet and moving forward.