This article does a deep dive into:
- The reasons behind 2021’s surge in plastic prices
- Predicts when prices might stabilize
- Advises companies with plastic packaging needs on what to do in the meantime
If you’re like most of our customers, you probably care less about how we got here and more about when things will get better and what to do in the meantime. If that’s you, feel free to skim the backstory and jump down to the parts of the article that answer your questions.
The 2021 Increase of Resin Prices
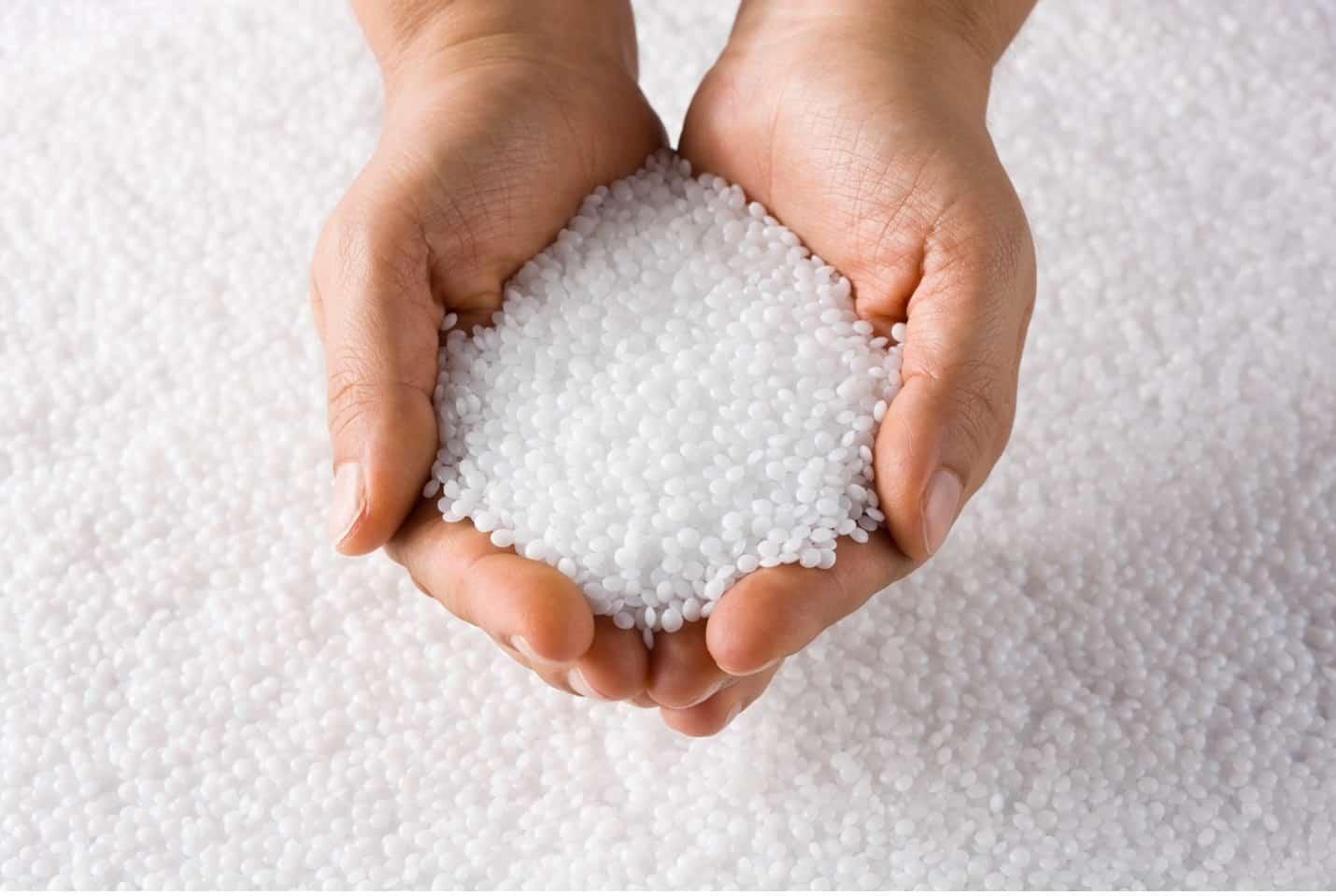
The pandemic has wreaked havoc on the historically stable plastic resin industry. Disruptions in the global supply chain, increasing demand for plastic packaging materials, and plastic production shutdowns have led to a severe spike in the price of plastic goods. As a provider of many different types of packaging materials, including plastic packaging, these trends have hit our customers hard in the wallet. At the time of this writing, the cost of plastic materials has risen approximately 40% for some of our customers.
What Caused the Resin Shortage of 2021?
There are several reasons for the current resin shortage. As Summit Director of Sales Greg Ong put it, this “perfect storm hitting the plastic industry is actually ‘a couple of perfect storms’ combined.”

Reason #1: Freak Storms and Plastic Plant Shutdowns
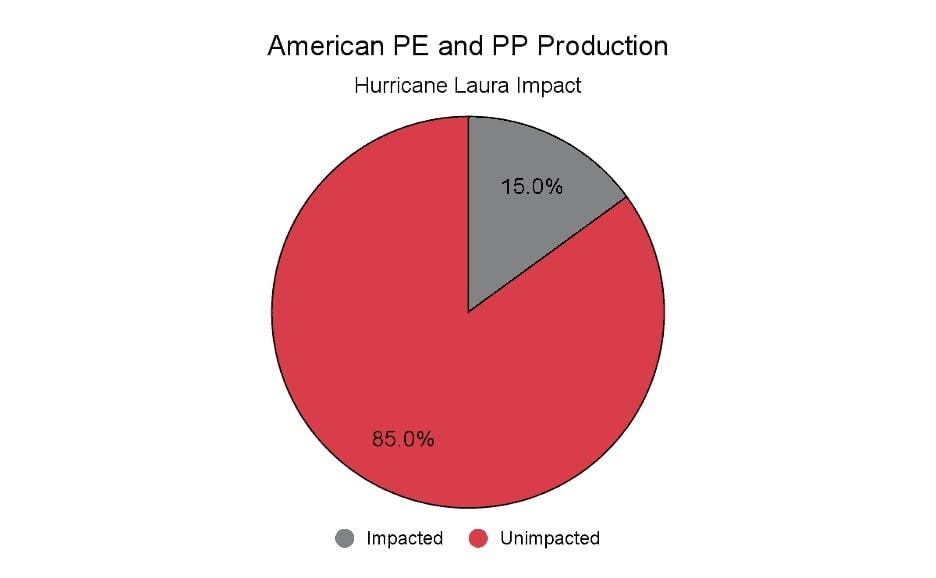
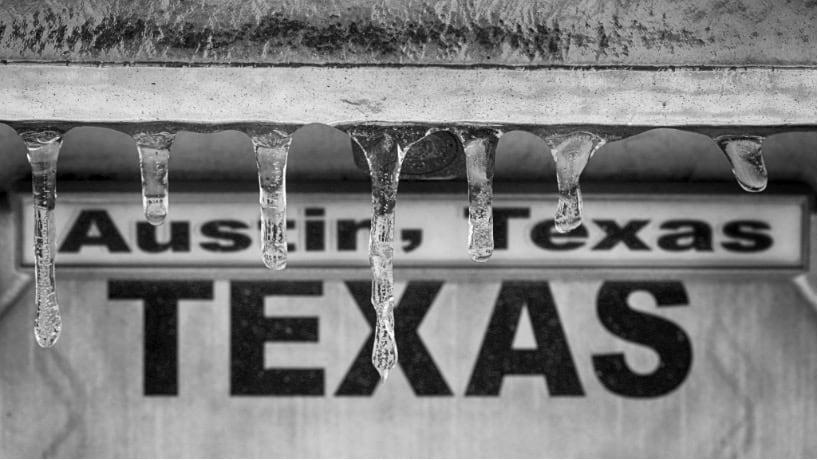
During the summer of 2020, Hurricane Laura brought extreme conditions that affected many big Gulf Coast polymer producers, including Chevron Phillips Chemical in Texas and LyondellBasell in Louisiana. They declared force majeure, a clause in most large contracts permitting deals to halt during extraordinary circumstances. The havoc caused by Hurricane Laura shut down a number of petrochemical factories so that practically overnight 15% of American PE and PP production was suspended. The effect of delayed production was scarce inventory of polyethylene (PE) and polypropylene (PP) supplies. At the time, experts estimated that it would take upwards of 6 months for Texas production to correct storm-caused imbalances and resume normal operations.
Then the Gulf Coast ‘freeze’ in Texas during February 2021 had another devastating impact on the plastics industry, shutting down major production facilities for polyethylene and polypropylene and decimating the power grid. The winter storm also halted production in the world’s largest petrochemical complex, causing a sudden shortage in almost 100 essential chemicals and derivatives used in much of Texas’s industry productions. Chevron Phillips Chemical and LyondellBasell were not the only resin producers impacted by the Gulf Coast storms. The freeze alone caused an estimated 12% reduction in US polyethylene production, with Exxon Mobil Corp., Royal Dutch Shell Plc, Westlake Chemical Corp., and Dow Chemical Co. also struggling to resume Gulf Coast operations.
Reason #2: The Infamous Suez Canal Cargo Ship Fiasco
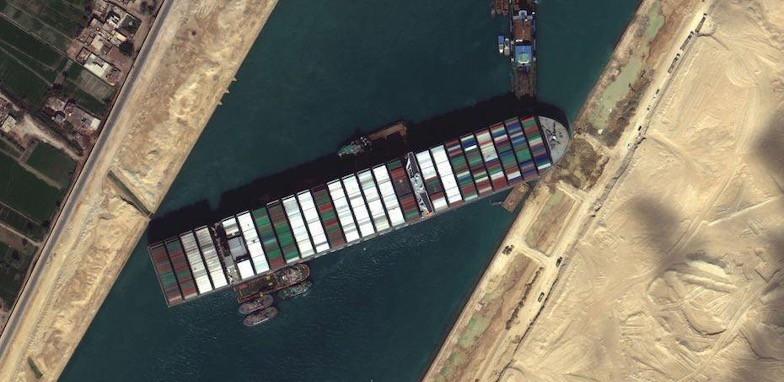
The plastics supply chain (and many other trade streams) were quite literally dammed by the March 23rd grounding of a container ship in the Suez Canal. This blockage delt another logistical challenge to the global plastic industry’s supply chain, since the Suez Canal is one the busiest shipping channels in the world.
Reason #3: Strained Relations in International Trade
Plastic commodity price rises from these shortages were made worse by international trade conditions. The recent spike in shipping costs from Asia damaged import arbitrage opportunities, reducing the plastic material entering America. And resin exports to Latin America added a strain to the already-limited US inventory, further raising plastic prices. Brexit custom shifts also negatively affected the global plastic supply chain. Trade between the EU and UK slowed because of port congestion resulting from strict Brexit-related customs checks and paperwork. These bureaucratic slowdowns led to significant delays in polyethylene, polypropylene, and polystyrene exports to the US.
Reason #4: COVID-19 Labor Shortages
Plastic production and distribution slowdowns are also attributable to Covid-19-related labor shortages. During the summer of 2020, quarantine lockdowns diminished the ability of factories to maintain inventory levels. Sanitary measures, worker reductions, and other Covid-19 precautions reduced production capacity significantly, creating a shortage of PE and PP inventory. Pandemic safety precautions also caused labor and trucking shortages at ports, starting a domino effect of slowdowns for resin distributors. The general results of these resin and plastic inventory (especially PE) constraints are widespread production delays and sharp price increases.
Reason #5: Demand for Plastic Packaging Up

The fourth contribution to ‘perfect storm’ conditions in the 2021 resin plastics industry was a huge increase in demand for plastics. Q1 of 2021 saw a further jump in demand for plastic packaging, but levels had already been high throughout the pandemic. The healthcare industry in particular has driven the need for plastic materials for personal protective equipment (PPE).
Of course, it’s not consumers themselves who are demanding plastic packaging. They are demanding and choosing online shopping options more and more, a well-established trend that took a huge leap forward during the pandemic. And what comes with your e-commerce purchase? Usually a little bit of plastic packaging. Globally, e-commerce plastic packaging produced $10.26 billion in 2020. It’s expected to double that number in 2021.
Increases in the Cost of Plastic in 2020 and 2021 by type
It’s not just plastic resin prices that have been high recently. Over the past two years, raw material costs were at record highs. Prices for steel, lumber, and plastic all skyrocketed as demand surged and production stalled.

Polypropylene Price (PP Price)
In January of 2021, US polypropylene prices rose from 13.5 to 96.5 cents per pound as a result of production shortages, import slowdowns, and exports to Latin America. In addition, the Mintec Global Packaging Index rose up by four points to 96.3, indicating an average cost of 55 cents per pound for plastic packaging materials. This was the highest plastic price since October of 2018, and while similar spikes were reflected across metal and paper markets, the most notable raw materials increase was in the plastics industry, with a market jump of 6.1% from the previous month and an average price of 65.32 cents/lb, more than double the 2019-2020 resin plastic price average.
PVC price changes
The extreme weather on the Gulf Coast has also dramatically altered 2021 plastic and resin prices. For example, polyvinyl chloride, or PVC was entirely offline for nearly a month during the Texas/Louisiana freeze. This had drastic implications as PVC is the world's third-most widely produced synthetic plastic polymer, used in construction for pipes, cable insulation, flooring, and roofing. And the US happens to be the world’s biggest exporter of this necessary material. As a result of Gulf Coast shutdowns, PVC export prices nearly doubled to a record high of $1,625 a ton. Other plastic prices reached record highs as well, including the price of polypropylene discussed above and the cost of high-density polyethylene, which is used in everything from shampoo bottles to grocery bags.
Polyethylene resin price (HDPE and LDPE prices)
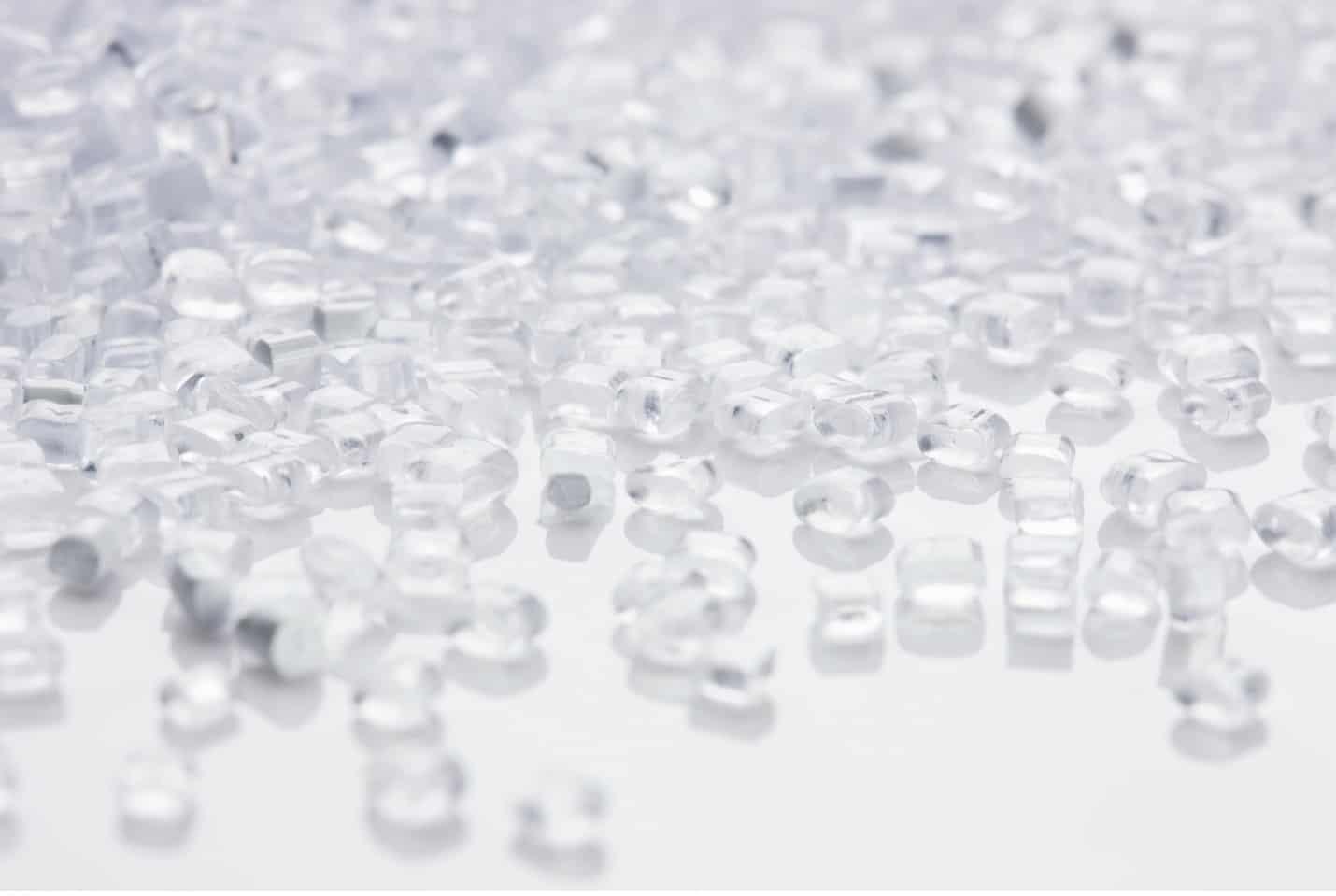
Brexit customs slowdowns also led to an increase in prices for EU high-density polyethylene (HDPE) and low-density polyethylene (LDPE). The cost for HDPE jumped by 8.3% in January to 68.98 cents per pound and the cost of LDPE rose by 9% to 77.52 cents per pound. So long as Brexit customs present obstacles to efficiency, HDPE and LDPE prices are expected to rise. On a national level, HDPE reached a record high of 77.25 cents per pound in March 2021. Many other regions are reporting prices currently reaching 82.00 cents per pound. Color HDPE jumped as well, from 18.91 to 23.63 cents per pound in March, a stark shift from just 7.38 cents/lb in March 2020.
Polypropylene (PP) has also climbed in price: from 5.69 cents/lb in 2020 to 18.44 cents/lb in February 2021, and 28.34 cents/lb in March 2021.
It is thought that Plastic prices have or will peak soon, and slowly plateau as producers and distributors work tirelessly to return operations to their normal, efficient, and stable states.
When Will the Cost of Plastic Return to Normal?
So, when will the price of plastics return to normal? That question might as well be posed to a crystal ball. If 2020/2021 has taught us anything, it’s that the future is unpredictable and that “normal” is elusive.
That said, Summit Director of Sales Greg Ong remains confident that plastic prices will likely stabilize by the end of 2021 summer, and ideally begin to return to normal levels by the end of the calendar year.
One known factor that will affect the plastic industry’s ability to rebound is the anticipated surge in consumer demand as vaccinated consumers venture out and spend their stimulus checks. Companies will likely not be able to respond to this spike, with supply bottleneck limiting long-term production. While those issues won’t be permanent, the resulting sudden price increase may have long-lasting effects on the US economy’s inflation rates.
Another anticipated price change is a 3-12.5% increase in cost for consumer goods like shrink film and other resin-based plastic flexible packaging supplies as a result of high costs in the resin market.
In late March of 2021, experts were anticipating a year-long recovery period for the plastics industry, meaning normalcy would resume in March of 2022, assuming there are no further interruptions. Whether that timeline is still feasible remains to be seen.
Global conditions will continue to drive plastic and resin prices upwards prior to decreasing- no matter when or if prices will ever return to normal. Despite varied recovery efforts, repairing our worldwide economy and trade systems will need significant time. If more major components to the global supply chain fail, expected recovery times will continue to be recalibrated. For that reason, it is important that consumers, suppliers, and everyone involved in the plastics supply chain remain vigilant and take preventative actions now. By staying well informed and working together, recovery will happen faster and more smoothly.
What Should Companies Who Need Plastic Packaging Materials Do in the Meantime?
If you need plastic packaging materials for your production, you have a few possible courses of action. The first is a strategy of stocking up supplies to avoid continued price hikes. We have encouraged companies to do this where possible, but with supplies being limited the amount that our vendors will allow any one customer to buy is often capped. Furthermore, bulk buying like this can sacrifice a lot of space and cash flow. Another option is to hold off on buying completely, speculating that the market is coming down soon. However, that option may cause issues down the road in terms of inventory and supplier relationships.

So, what should production managers and buyers do in the meantime to keep afloat? One tactical option is to establish a relationship with a local just-in-time (JIT) materials provider like Summit Packaging that knows the market and can aid in navigating the upcoming uncharted waters. Another good idea is to explore alternative packaging materials, structures, and thicknesses that might be cheaper but still appropriate for your product.
Companies with packaging needs should reduce uncertainty by dialing in forecasted production schedules and sharing that insight with their materials suppliers. Maintain clear and open communication with packaging vendors. The better companies can anticipate and communicate their needs, the better their JIT packaging company can serve them. Partnering with Summit can help maintain inventory without crowding production spaces, ensure that materials arrive in a very timely way, and resolve any availability or pricing issues by finding alternative solutions.