Downtime — whether planned or unplanned — is a fact of life. So while you can’t eliminate it, you can reduce downtime with a preventative maintenance program.
Think of it this way: you probably don’t drive your car until the engine seizes up. Instead, you get regular oil changes and perform other maintenance so you don’t get stranded on the highway. Same with your equipment. Regular maintenance makes it run better. Plus, timely routine fixes are always preferable, and usually faster, than major repairs or emergency maintenance calls that bring your operations to a halt.
Establishing and following a consistent process for servicing your machines extends equipment life, increases safety, decreases downtime, and improves your operations.
The 3 Types of Planned Downtime
There are three types of planned downtime: operational, sanitation, and maintenance. Operational includes the daily set-up and breakdown of the equipment including any material, configuration, or product changes during or between shifts.
Sanitation involves cleaning the equipment along with operational and maintenance downtime. Whether it’s your operators or your sanitation crew who assemble or disassemble the machine, be sure to perform post-cleaning lubrication for best results.
Maintenance downtime can be either emergency or preventative, and both can be categorized as repairs or maintenance.
Preventative Maintenance Tips
It’s important to stress that preventative maintenance is a team sport. A successful program involves upper management, production, maintenance, and especially sanitation all working together.
Below are some tips for creating or improving your preventative maintenance routine:
- Ongoing training is critical. Train your maintenance staff and operators so they know what the equipment can and can’t do. Make sure everyone on the team is familiar with signs of wear and how to make reasonable adjustments. Similarly, your sanitation crew needs to know how to clean items without damaging them. This requires consistent training and regular check-ins.
- Grease, lube, and oil. Regular lubrication helps extend the life of your equipment and improves performance.
- Keep wear parts on hand. Bearings, springs, and guides are often there to protect major (and expensive) components so replace them before you have issues. Having wear parts available, and knowing how to install them, keeps you running.
- Read the manual. This might seem obvious, yet many people forget to do it. But it’s worth taking the time. Most manufacturers offer directions on wear and tear, lubrication schedules, and other information you can use.
- Start slow and ramp up. If you’re looking to introduce or improve your current maintenance program, it can be overwhelming at first. So start small. approach each piece of equipment individually and don’t move on until your team is comfortable with maintaining that machine. This also helps you improve your processes as you go along.
- Review your SOP. Routine maintenance is a great opportunity to review your standard operating procedures, HACCP issues, and safety policies.
- Watch the numbers. Parts and labor are an investment. But a good PM program should also include an expectation of savings. Setting savings goals can help you set accurate budgets for parts and labor while revealing opportunities to further cut costs.
- Count the grease fittings. A useful training tip is to tell the technician doing the lubrication how many fittings there are and then ask them to find them. This gets them familiar with the machine and allows the trainer to follow up and answer questions.
Finally, don’t forget about one of the most important parts of any preventative maintenance routine: consistency. Because whatever type of equipment your company uses, creating and following a maintenance plan is a sure way to get the most from your investment.
For more advice on running a successful preventative maintenance program, call Summit at 253-858-4040 to chat with an expert.
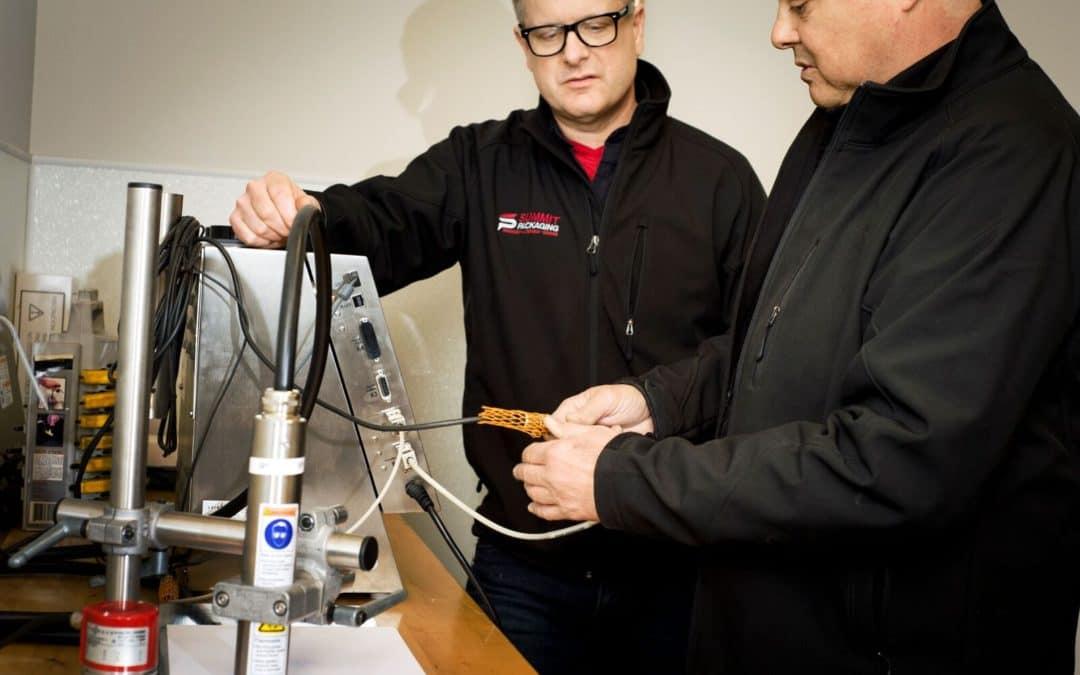