As these exciting technologies advance, analyzing new trends in industrial automation has become increasingly essential for companies looking to stay ahead of the curve, and explore new possibilities. From robotics to AI (artificial intelligence), there are myriad options available to improve efficiency and reduce costs. But with so many new options out there, sifting through the latest trends in industrial robotics and trying to predict future trends in industrial automation to make the right investments for your production business has become a Herculean effort–but one that our engineering team is happily doing for you.
In this article, we'll break down the industrial automation process, sift through those options with you and discuss the various technologies available, weighing their advantages and disadvantages. We'll also explore how organizations like yours can use them to increase productivity while reducing costs and how you can prepare for potential challenges that may arise from implementing these solutions.
The Role of Robotics In Industrial Automation: Cobots vs Robots
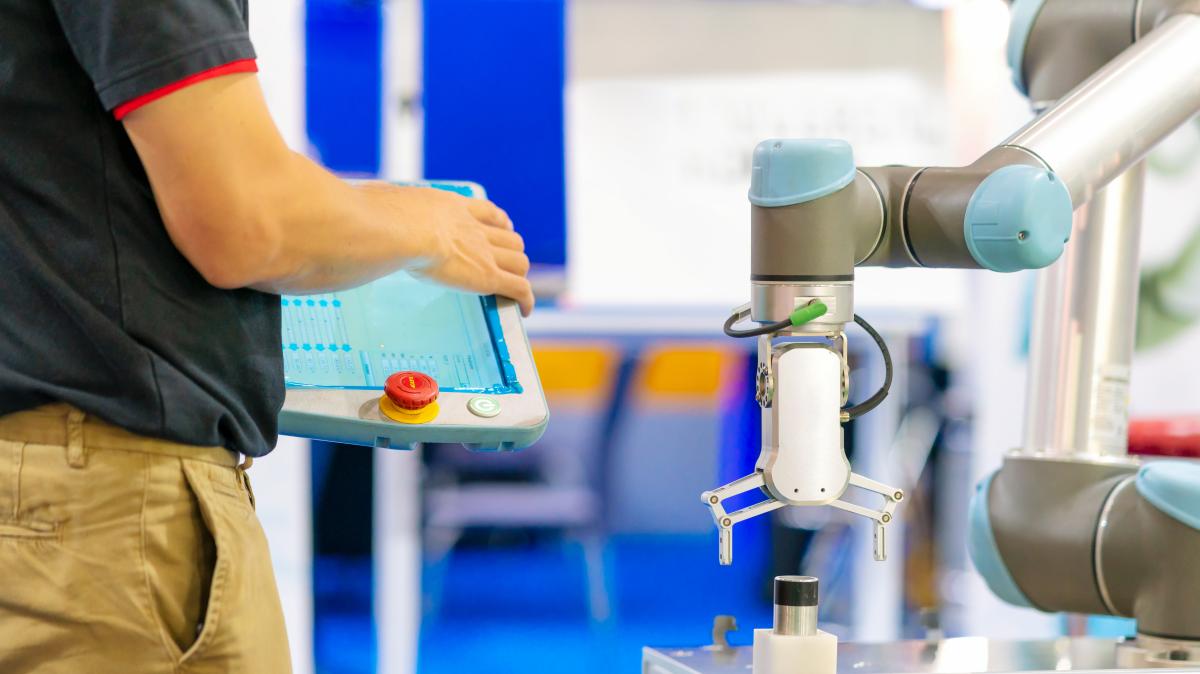
To understand the role of robotics in recent innovations in industrial engineering it's important to understand the difference between robots and “cobots” (collaborative robots). Collaborative robots are the biggest industrial automation trend in 2023 and they are likely to remain the biggest trend throughout the 2020s, particularly when it comes to packaging automation. Here are a few of the benefits that collaborative robots could bring to your industrial business:
- Flexibility
- Safety
- Cost Effectiveness
- Improved Productivity
- Ease of Use
So, what exactly are these robots? A succinct cobot definition is that collaborative robots, or “cobots” for short, are a type of robot designed to work safely alongside humans in a shared workplace. While traditional industrial robots operate behind safety barriers to prevent physical contact with humans, cobots do not need to be kept behind a barrier. This is because cobots are equipped with advanced sensors and software which allow them to detect human presence, movement, and touch. Once a human is detected in its vicinity, many cobots will slow down their movements to prevent physical contact. Additionally, many cobots will stop movement altogether when their sensors detect that a human is touching them, drastically reducing the chances of injuring their human coworkers. Safety aside, why are collaborative robots making such an impact on industrial automation?
For starters, cobots can be programmed to perform a variety of tasks. For example, at Summit we have designed systems to have a single collaborative robot package products into boxes and then, once they are filled, load those boxes onto a pallet. This is because cobots are effective at what is called “pick and place”, meaning they can easily move items from one location to another. Cobots are also excellent at assembly tasks like inserting components, screwing down items, riveting, and attaching parts. Not only are they more precise and efficient, they don’t get carpal tunnel syndrome or strain their backs from repetitive labor like their human coworkers. Additionally, cobots have a higher accuracy in detecting defects in products, parts, or industrial machinery around them. In fact, vision system sensors on the end of their arms allow cobots to verify the quality of a part or a product before they even pick them up. With the help of robotics, manufacturers can make decisions based on data produced from smart sensors with greater accuracy and be more agile when responding to dynamic market conditions.
The Impact of Vision Systems on Automation
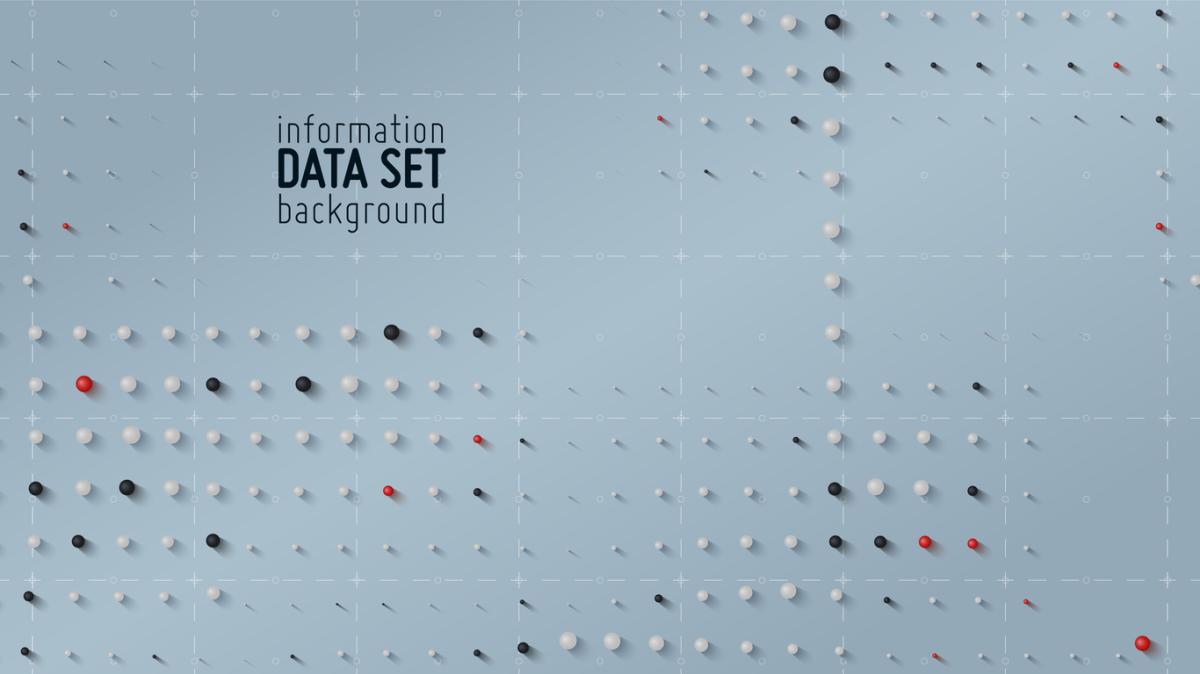
Vision systems are the second biggest industrial automation trend in 2023 and beyond. Vision systems are a technology that utilizes cameras, sensors, and software to inspect or analyze parts and products on a manufacturing or production line. How does this technology work? Vision systems can be broken down into two main parts:
- sensors (or cameras)
- algorithmic software
A collaborative robot’s sensors capture images and its algorithmic software processes those images in real time. Vision systems enable cobots to not only inspect products faster than their human coworkers, but they give industrial companies the chance to remove human error altogether. At Summit Packaging, we can integrate vision systems at any point in a process, whether it be inspecting raw materials or products as they're moving along a conveyor to inspecting a finished box or a full pallet at the end of the line.
The Impact of Autonomous Mobile Robots

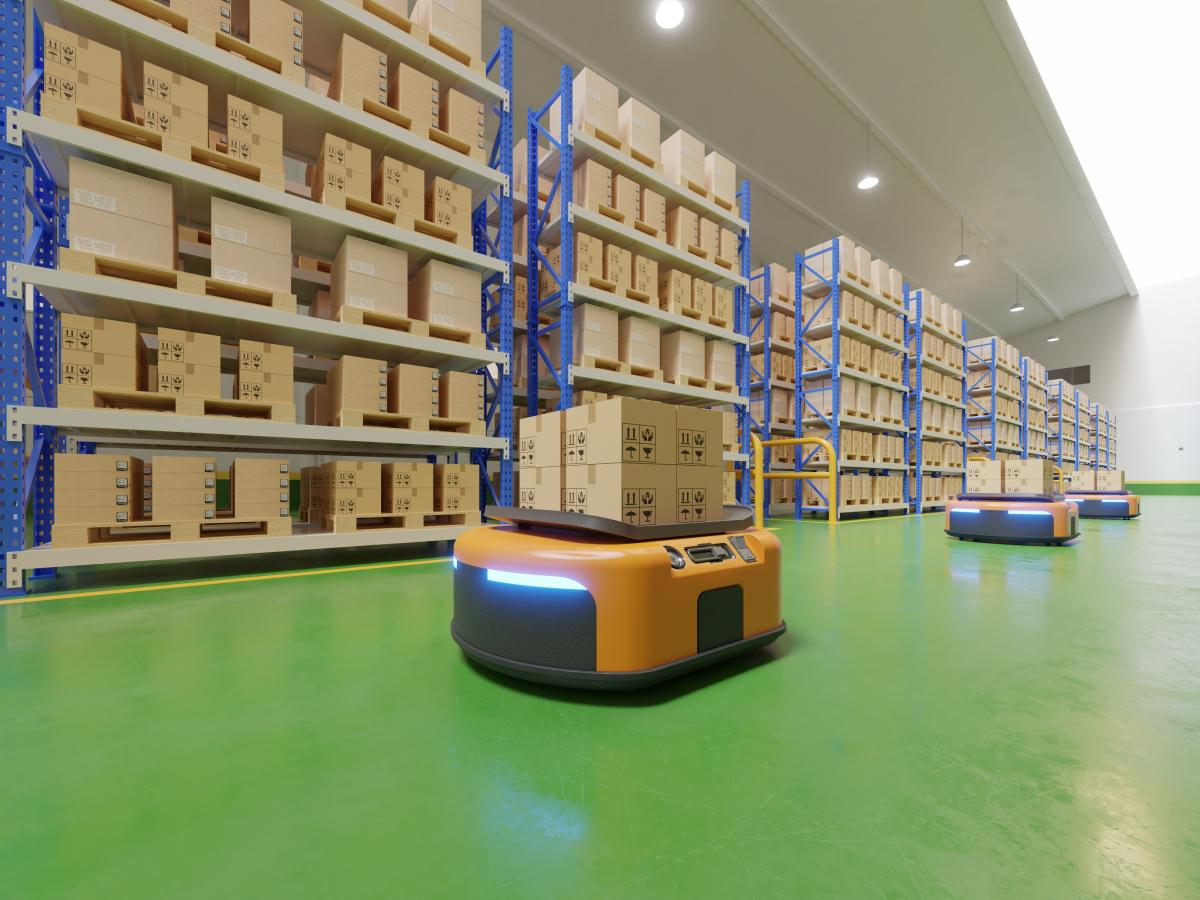
Autonomous Mobile Robots, or AMRs, are the third biggest industrial automation trend we’ve seen so far in 2023. So how do autonomous mobile robots work? In simplest terms, an AMR is a robot on wheels that zips around a production floor to complete a variety of tasks. AMRs are a type of portable robot designed to navigate efficiently and operate autonomously across an industrial space. With a suite of sensors to collect information about their environment coupled with powerful computing and decision-making capabilities, AMRs navigate dynamic and unstructured environments like a pro.
Due to their similarities, AMRs are often confused with Automated Guided Vehicles or AGV Robots since they too move around in an industrial space and complete tasks. AGVs have been around since the 1950s, albeit in a cruder form. AMRs, however, are the new kid on the block. What makes AMRs and AGVs distinct? The differences between AMRs and AGVs come down to two crucial factors:
- flexibility
- adaptability
AGVs are designed for repetitive tasks and can only move by following a line of magnetic tape from one end of a factory to the other. AMRs, however, can move around in any direction just like their human coworkers. They are also able to navigate around obstacles, create their own paths, and change their behavior based on a real-time sensory analysis of changes in their environment.
To install AGVs in your packaging facility you will need to build a large conveyor line, making AGV implementation a far more costly, complex, and lengthy process than utilizing AMRs which can zip around a facility without needing an expensive conveyor line. This is one of several reasons why AMRs are quickly becoming a more popular option for packaging companies to maximize efficiency.
Industry 4.0
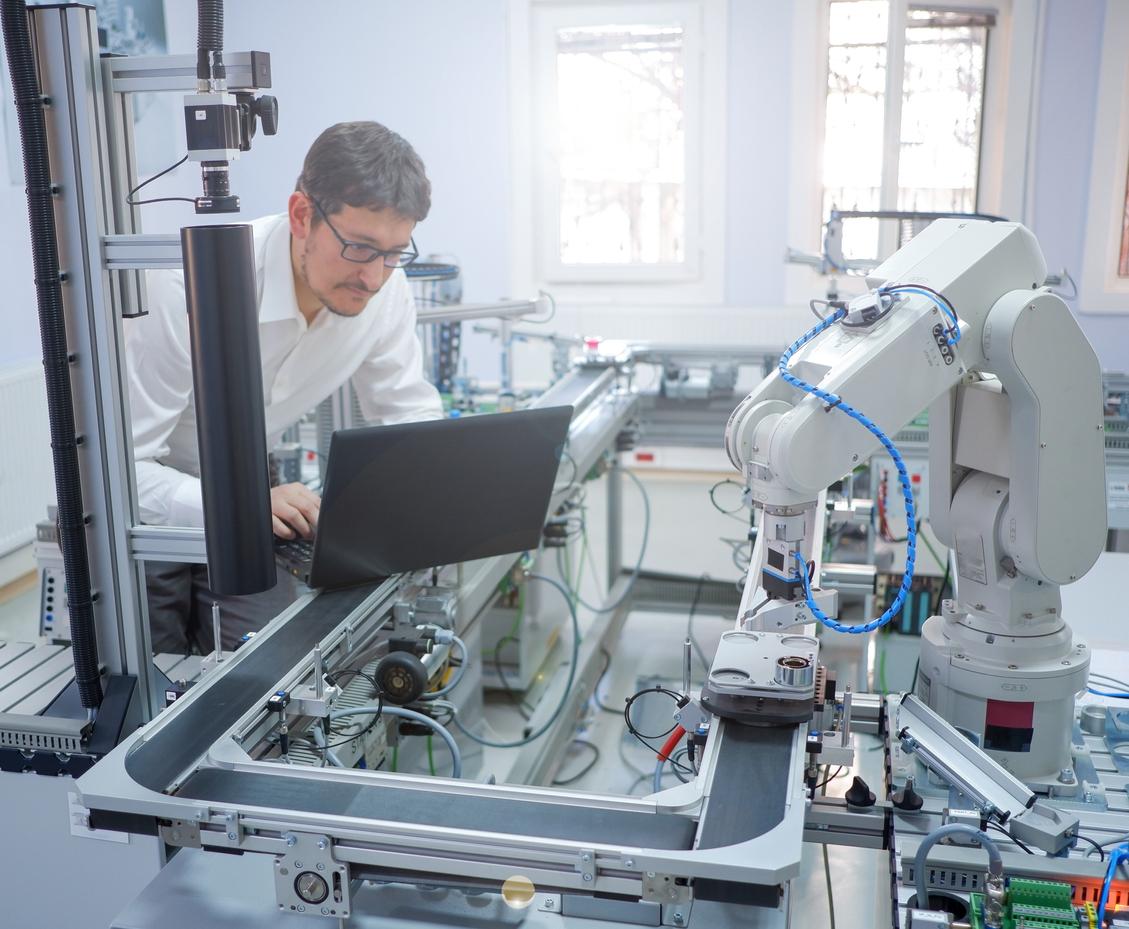
Industry 4.0, which is short for the fourth industrial revolution and is often called “smart factories”, is another of the biggest industrial automation trend we’re seeing in 2023. Industry 4.0 refers to production facilities that have integrated advanced technologies like AI, big data, the Internet of Things or “IoT”, and robotics which are all working together to increase productivity, monitoring capabilities, and flexibility. While these technologies have each been developed by different people and across different time periods it is their interconnectivity, or their use in tandem, in recent years that has begun a new industrial revolution. Now that these machines and systems are all connected to each other and to the internet, industries can achieve real-time data monitoring and communication on a grand scale.
The automated future of industry is built on the foundation of machine learning and automation. The convergence of these two technologies has enabled unprecedented control over operations. One of the most significant applications of machine learning and automation lies in predictive analytics. By analyzing data from sources such as AC power usage, companies can identify patterns that allow them to anticipate changes from the factory floor to global markets before they happen.
We’ve discussed how important recent innovations in robotics have been to the latest industrial automation trends. But what about AI, big data, and IoT? Let’s discuss the critical role these emerging technologies play in industrial automation trends.
The Impact of AI on Automation
By harnessing the power of AI, business owners can now manufacture finished products with ease and accuracy while running their manufacturing facilities essentially on autopilot. This is where the key difference lies between traditional and automated manufacturing: O PAS-certified products can now be made without human intervention. This means that businesses have access to a streamlined production process that eliminates waste, increases efficiency, and ultimately reduces costs. From raw materials to deliverable products, AI-powered systems can enable manufacturers to produce more in less time than ever before and help them keep up with the demand for faster delivery times, as well as track and analyze data points from their industrial floor for further optimization.
The Impact of Big Data on Automation
Think of big data as a deep well of insights, enabling companies to keep up with ever-changing industrial automation trends. With real-time data streaming in, AI or machine learning algorithms can quickly identify patterns and anomalies, and predict when mechanical failures might occur. This collection of data occurs at each point in the production process from machines, sensors, and other sources and it provides companies with valuable insights into their customers’ needs and preferences, allowing them to optimize their production for maximum efficiency.
The impact of big data on automation is far-reaching since smart factories use it to monitor and adjust their manufacturing process, leading to increased operational efficiency. Intelligent business process automation also relies heavily on big data to drive production processes while improving overall quality standards and increasing customer experience and satisfaction.
The Internet Of Things and Automation
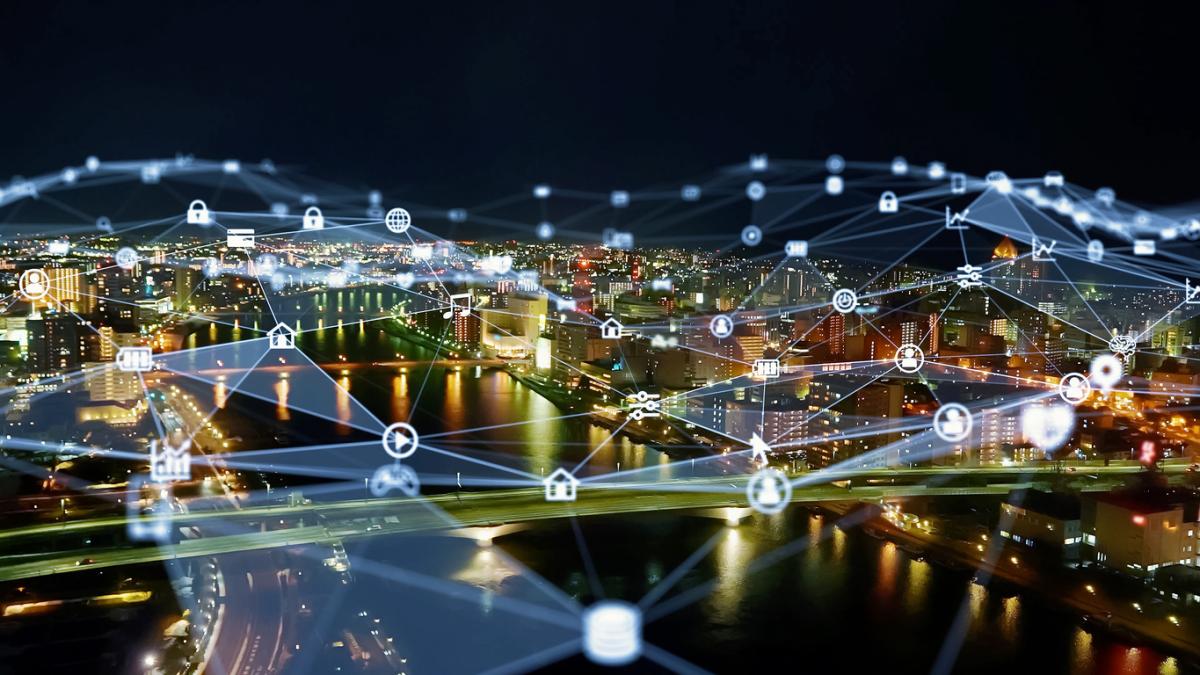
Where does the Internet of Things (IoT) come into automation? By connecting the entire manufacturing operation. From cloud computing to edge computing platforms to sensors to navigation capabilities, this interconnection has enabled manufacturers to achieve peak efficiency in their production process, leading to unprecedented levels of control and accuracy in their industrial applications.
Manufacturers are now able to monitor the whole manufacturing environment with ease via IoT-enabled technology. They can transparently track each step of the process from raw materials to finished products while gaining increased insight into their operations. This helps them identify areas where they can save time or improve quality and safety standards. Logistics companies have also taken advantage of this technology, using it to optimize shipping routes and ensure timely delivery.
Now that we’ve covered the most important technological breakthroughs that have brought about Industry 4.0, let’s take a look at other industrial automation trends that will reshape our future.
Micro-Fulfillment Centers and Automation
With micro-fulfillment centers or small-scale storage facilities, coupled with automation, companies have a real opportunity to get ahead of the competition by increasing productivity and customer satisfaction while minimizing labor and shipping costs. Let's take a look at the impact micro-fulfillment centers and automation are having on supply chains, production facilities, and human workers:
• Supply Chains: Automation products have allowed companies to track their raw materials in real time, thereby significantly reducing maintenance costs and machine downtime.
• Production Facilities: Mobile robots are now being used to automate manufacturing processes, thus increasing output while decreasing labor costs.
• Human Workers: Industrial automation has allowed for more efficient use of human labor, with workers often handling tasks that require superior decision-making capabilities or manual dexterity.
Warehouse Drones and their Uses

From a security perspective, warehouse drones, or unmanned aerial vehicles (UAVs), can help monitor and maintain a secure perimeter around warehouses. UAVs are an excellent addition to the industrial factory automation process as they can reduce supply chain disruptions. UAVs can be used to track inventory levels in real-time, enabling manufacturers to better plan for shipment times and ensure timely delivery of goods. Additionally, they can be programmed to execute various tasks such as sorting items or delivering goods directly from one location to another. This could save companies time and money by eliminating the need for manual labor or expensive transportation costs.
Augmented Reality and Automation
Augmented reality (AR) is a trend that Flexware Innovation is analyzing for its potential to enhance automation processes. Here are three ways in which augmented reality is driving innovation in industrial automation:
- Automation processes can be monitored and improved through data analysis provided by AR technology.
- AR allows for increased accuracy while performing maintenance, repairs, inspections, etc.
- The use of AR can reduce human error by providing user guidance and visual assistance during complex tasks.
Cyber Security and Automation
We've all heard stories of companies who failed to take cyber security seriously and paid for it dearly with compromised data and millions in losses. To stay ahead of the curve when automating your processes, you need to consider security from the outset. Here are some key steps:
• Establish secure networks and protocols for communication between robots and machines
• Use secure authentication techniques to protect access to systems
• Monitor processes for suspicious activities or unauthorized access attempts
No matter what level of automation you're aiming for, cyber security needs to be top-of-mind throughout the process. An unsecured system can leave your business vulnerable to attack, leading to costly downtime or worse - stolen intellectual property or customer data. Taking steps now will ensure that your automated processes remain safe and secure in the future.
Prioritizing Sustainability in Automation
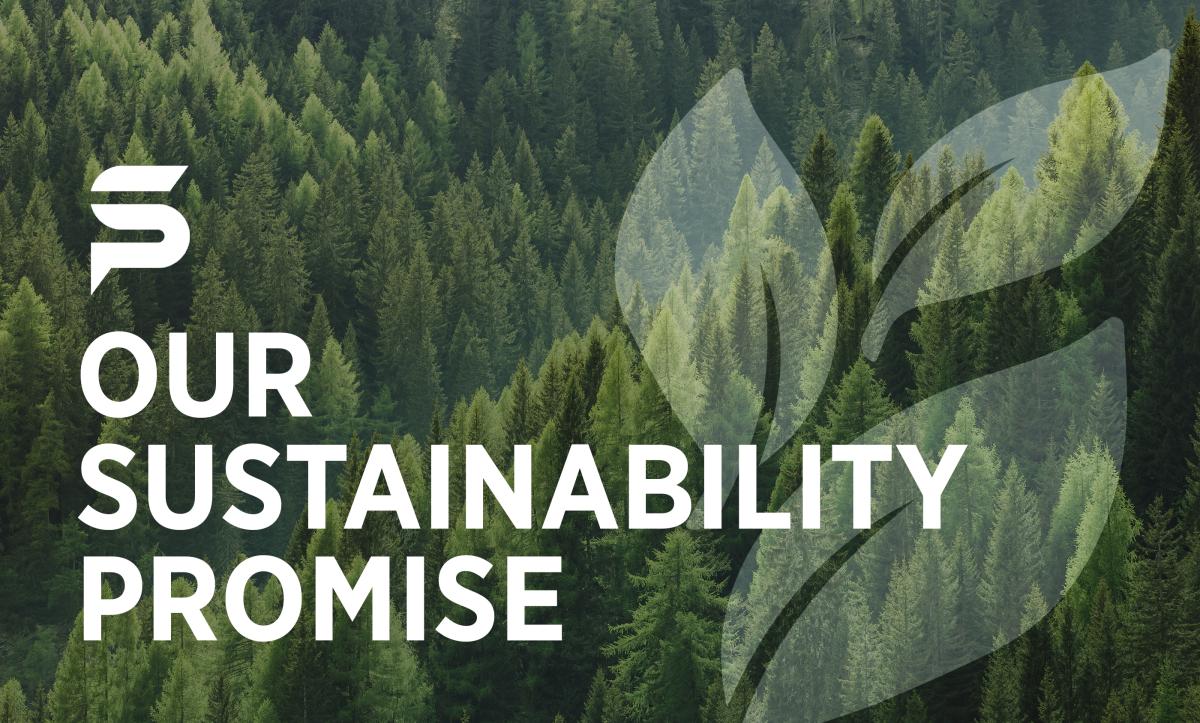
Advancing technologies such as the digitalization of manufacturing and machine vision systems have streamlined manufacturing and, in the process, cut down on waste, power consumption, and emissions. These cutting-edge technologies have given companies the opportunity to minimize their environmental footprint. One of the biggest current trends in industrial automation is the increase in sustainable practices as it is critical for improved efficiency, and healthy practices.
If you're thinking about implementing automation in your packaging facility, you'd probably like a partner. Summit Packaging's team has the knowledge and expertise to implement these technologies to help our customers make the right decisions to maximize their production efficiency, reduce cost, as well as improve product quality.