Article Main Points
- Elevated minimum wage in regions like Washington state increases competition for skilled labor.
- Remote work preferences in other sectors divert potential manufacturing workers.
- Younger generations show less interest in traditional factory roles, impacting recruitment.
- Technological advances in automation reduce the demand for human labor in manufacturing.
- Nationwide trends reveal a severe, enduring workforce shortage across the U.S. manufacturing sector.
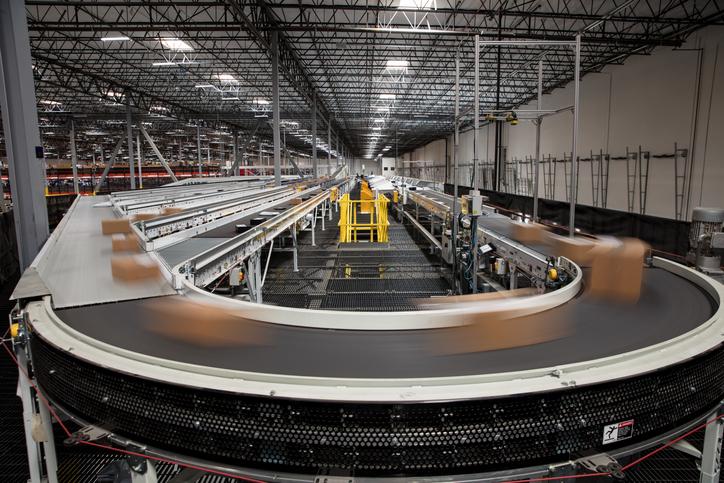
The 2024 Labor Shortage
The industrial packaging manufacturers in the Pacific Northwest confront a critical workforce deficit. This severe shortage of personnel threatens the sector's future unless decisive measures are implemented. Companies now prioritize innovative hiring methods to attract diverse applicants and invest heavily in comprehensive training initiatives.
In response to the scarcity of workers, technological advancements, such as automation and sophisticated production techniques, play a crucial role. These technologies reduce reliance on human labor. Although these solutions require significant initial outlays, they ensure long-term viability by boosting efficiency and reducing running costs.
To effectively address the workforce shortage, the sector must adopt a holistic strategy that combines strategic recruitment, intensive training, and technological advancement. This approach will enable the industry to overcome current challenges, ensuring its resilience and ongoing expansion in a competitive environment.
A Nationwide Crisis
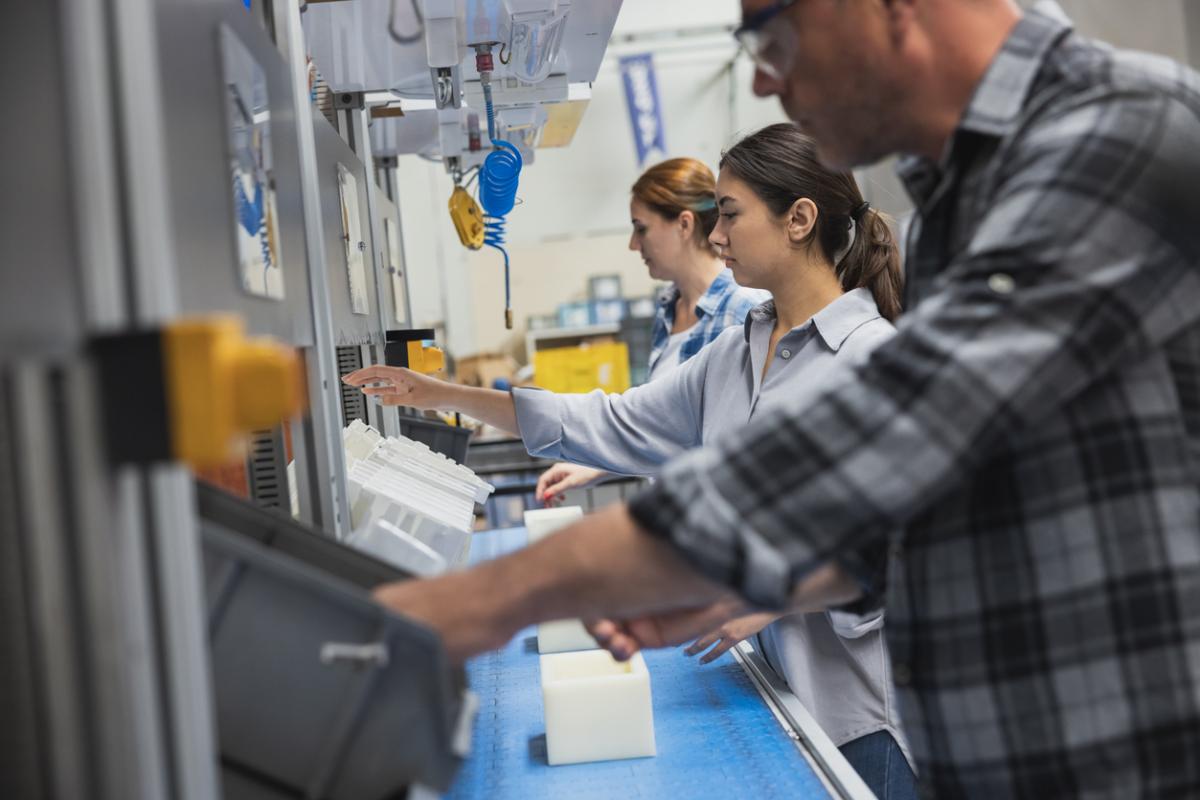
The U.S. confronts a severe workforce shortage, especially in its manufacturing industry, with an unemployment rate at a mere 3.9% as of March 2024. This dilemma not only challenges the sector but also threatens economic stability. The Manufacturing Institute projected in 2021 that more than 2 million manufacturing jobs could go unfilled by 2030.
Firstly, the lack of workers elevates salaries and operational expenses, undermining the international competitiveness of U.S. factories. Next, enterprises face difficulties in both recruiting and maintaining employees, which destabilizes the industry. Furthermore, the introduction of advanced training initiatives and collaborations with academic bodies is critical to preparing a new generation of employees. Lastly, the necessity for governmental strategies that promote vocational training and attract individuals to industrial careers is pressing.
Efforts from both corporate leaders and policymakers are essential to launch effective educational programs and create supportive policies. These actions aim to ensure the endurance and expansion of the manufacturing sector during these demanding times.
Zooming in on the Pacific Northwest
Yes, the Pacific Northwest is grappling with a labor shortage, particularly in sectors like manufacturing and aerospace. In 2024, the elevated minimum wage of $16.28 per hour in Washington state, one of the nation's highest, exacerbates this issue by increasing competition for skilled labor.
To address this, enterprises are prioritizing employee retention strategies. They are introducing enhanced training initiatives to sharpen competencies and foster worker commitment.
Additionally, the implementation of telecommuting policies broadens the labor pool by including individuals from secluded areas who can work from home. Furthermore, many organizations are integrating automation technologies to lessen reliance on human workers and enhance steadiness in operations.
These measures collectively help alleviate the labor shortage's impact in this crucial area.
The "All-In" Cost of Labor
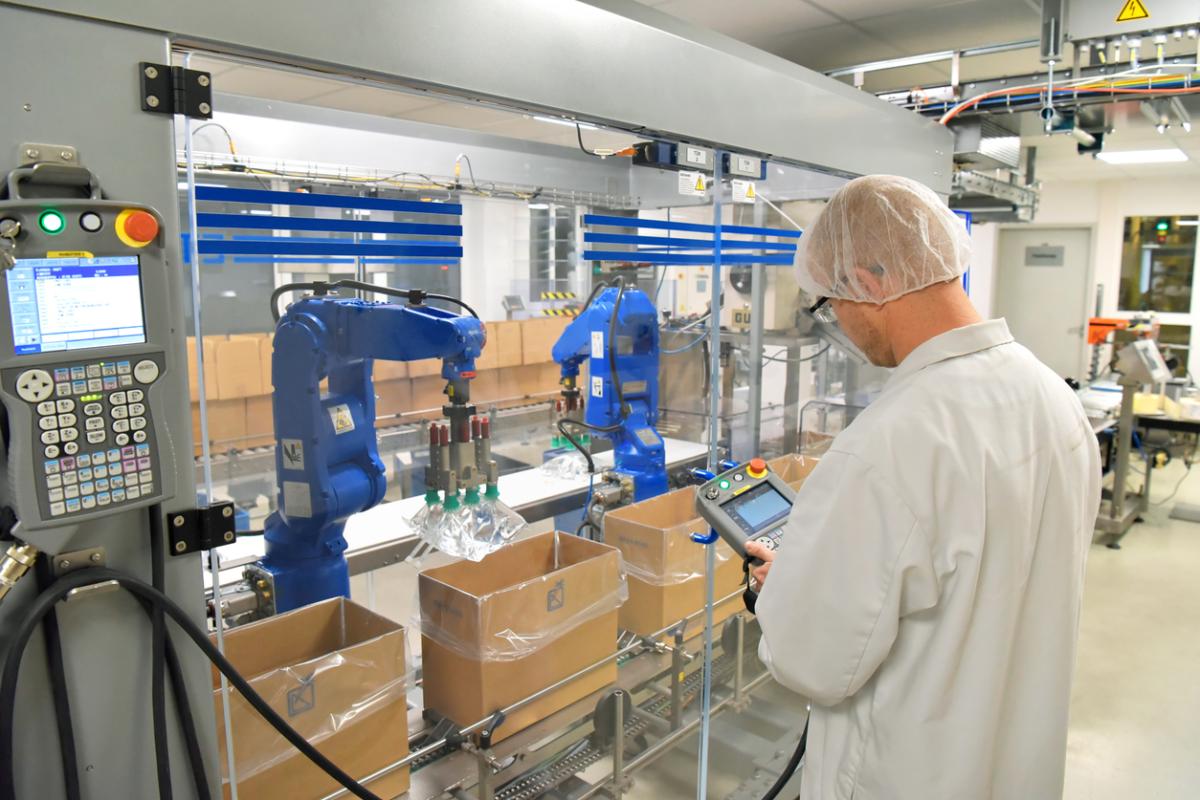
Companies tackle the comprehensive cost of labor through strategic planning and innovative methods. These costs include not just wages but also perks, extra payment for additional hours worked, mistakes due to human factors, and expenses for training and educational programs.
Here are four primary strategies:
- Expenditure Review and Workforce Productivity: Enterprises conduct detailed expenditure reviews to grasp the full costs tied to each staff member, covering both direct and indirect expenses. This aids in better budget oversight and promotes workforce productivity, optimizing worker output and reducing waste.
- Capability Enhancement Initiatives: It's crucial to boost capability enhancement. By educating staff to manage multiple responsibilities and regularly updating their capabilities, enterprises can diminish the frequency of new recruitments and lessen the errors made by staff, thus reducing educational expenses over time.
- Staff Retention Approaches: Applying effective staff retention approaches helps lower the costs associated with staff turnover. These approaches encompass competitive earnings, comprehensive perks packages, and the creation of a supportive workplace atmosphere.
- Technological Automation: Technological automation is key in undertaking repetitive duties, decreasing the need for a large workforce. This not only reduces costs linked to human mistakes and additional hours but also enables staff to concentrate on more intricate and value-adding tasks.
A Real-Life Example
A recent event for one of our new food processing customers highlights the challenges of employee reliability in manufacturing. After hiring five workers in one day, only two returned after lunch, and just one appeared the next day.
This situation highlights several critical issues:
- High turnover: Quick loss of workers hampers production timelines and volume.
- Training inefficiencies: Training costs become wasteful when workers depart soon after.
- Recruitment difficulties: Continually sourcing and recruiting new labor depletes resources.
- Team morale: Frequent turnover dampens the spirit of permanent staff.
- Financial strain: The cycle of employing and training new labor imposes financial burdens.
These challenges might mirror your own. Recognizing these elements can guide you towards more effective recruitment strategies and potentially integrating more automation to reduce these pressures.
To tackle these issues, companies must adopt several strategies. First, effective hiring practices are key. These should focus not just on abilities but also on a good match with the company's ethos, which can significantly affect worker retention. A strong company ethos creates a sense of community and purpose, encouraging workers to stay.
Moreover, comprehensive training schemes are crucial. They should ensure workers are not only skilled but also valued and involved. These schemes need regular updates to meet industry needs and maintain worker interest.
A Trend with No End in Sight
Unfortunately, the current trends suggest this problem isn't going away anytime soon. In recent decades, there has been a cultural shift towards higher education and less emphasis on vocational trade schools, leading to a shortage of skilled workers in the manufacturing sector.
To grasp the intricacies of this problem, consider the following points:
- Desire for Remote Work: The appeal of working remotely in other industries attracts potential workers away from manufacturing, which generally demands physical presence at the plant.
- Automation's Role: Although automation aims to bridge some gaps, its adoption is gradual and the requirement for skilled personnel to oversee automated systems increases the need for specialized training.
- Need for Skills Training: There is an urgent requirement for improved training initiatives that are in line with contemporary manufacturing technologies to draw and keep workers.
- Generational Preferences: The younger cohorts are less drawn to traditional roles in factories, swayed by their perceptions of the sector and alternative career paths that appear more secure or appealing.
These factors, combined with fierce competition within the sector, create a difficult environment for hiring in manufacturing, indicating that addressing this worker deficit will necessitate thoughtful, diverse strategies.
Supply vs. Demand: A Vicious Cycle
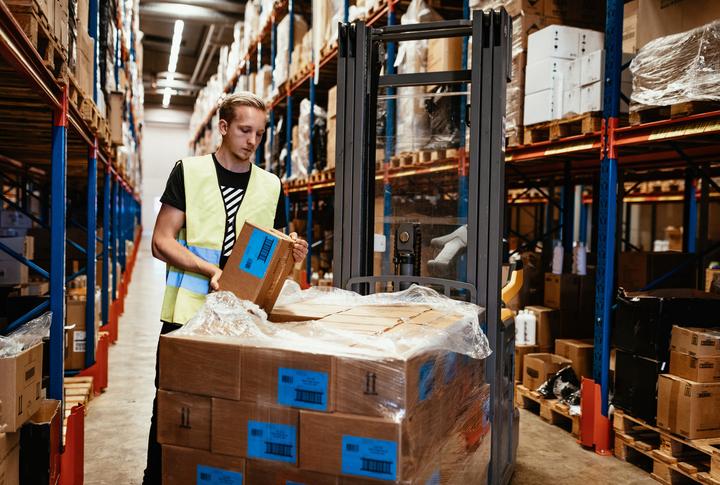
Wages rise as companies compete for a limited number of skilled laborers, deepening the cycle of increased production expenditures and potentially elevated prices for consumers. This pattern stems from the basic market forces of supply and demand. With fewer people available and skilled in specific fields like aerospace and industrial packaging, the pressure on wages increases. Businesses must offer higher pay to attract and retain essential employees, affecting their financial plans.
Here's a closer examination:
- Higher Employment Expenses: Essential wage increases elevate company costs.
- Increased Commodity Costs: These necessary wage hikes lead to raised prices of goods.
- Decreased Marketability: As goods become pricier, they lose appeal against more affordable alternatives.
- Possible Sales Reduction: A drop in competitiveness might lead to fewer sales, worsening financial conditions.
- Challenging Reinvestment: Narrower profit margins complicate funding for innovation and efficiency, potentially hindering expansion.
Understanding this cycle is crucial for devising effective strategies to mitigate its effects. Many in the industry face this widespread challenge.
The growth in salary costs shows in the manufacturing costs. As these rise, businesses face tough choices about pricing strategies, which may influence their competitive standing in the market. Balancing cost control with attracting labor becomes a key issue. Without enough employees, the ability to keep up production volume and standards falls, jeopardizing the market presence of companies in the sector.
This relentless cycle of climbing wages and manufacturing costs plays a major role in the persistent labor shortage, underscoring the urgent need for thoughtful human resource strategies and creative labor solutions in manufacturing.
It Doesn't Have to Be This Way
Labor shortages present a distinct moment for entity growth and innovation. Enterprises can adopt automation technologies to efficiently manage workforce challenges. This shift not only maintains production but also enhances productivity.
In the realm of industry, automation marks a profound shift, setting new benchmarks for manufacturing efficacy. Consider these four compelling motives for enterprises to embrace automation:
- Decreased Workforce Reliance: Automation leads to less dependence on a limited workforce, thus stabilizing output rates and mitigating the effects of high employee turnover.
- Heightened Output Efficiency: Mechanical systems operate incessantly, eliminating the need for human breaks or shifts, thereby increasing production and satisfying peak demand without additional workforce costs.
- Superior Quality and Uniformity: Devices offer precision and uniformity, surpassing the occasional inconsistencies of human labor, which results in superior product standards and minimal defects.
- Extensive Financial Savings: Although the initial investment in automation systems is considerable, the long-term financial benefits from reduced workforce costs, diminished training expenses, and fewer operational inefficiencies can be transformative, fostering significant expansion opportunities for enterprises.
Adopting automation not only resolves immediate workforce shortages but also prepares enterprises for sustained growth in a dynamic market environment.
Conclusion
To sum up, the 2024 manufacturing labor shortage represents a complex tapestry woven from diverse socioeconomic threads.
This crisis, characterized by regional disparities and evolving labor expectations, underscores the urgent need for adaptive strategies.
It illuminates the stark reality that industry sustainability hinges on addressing both wage competitiveness and job appeal.
Through strategic intervention and innovative workforce engagement, the potential for reversing this trend exists, offering a beacon of hope in maneuvering through these turbulent waters.
In the next article, we'll explore how automation equipment can be a powerful tool to bridge the labor gap and ensure your business continues to thrive. We'll delve into how companies are successfully implementing automation solutions and how Summit Packaging can help you navigate this transition.
In the meantime, if you're facing labor shortages and are curious about how automation can help, don't hesitate to reach out to our team of experts!