A successful maintenance program involves supporting your people as much as servicing your equipment. Summit Packaging’s goal is to train your team to be as self-sufficient as possible by building your expertise and giving you the tools to properly maintain your machines to get the most value. Below are four key ways Summit supports your maintenance and operations teams.
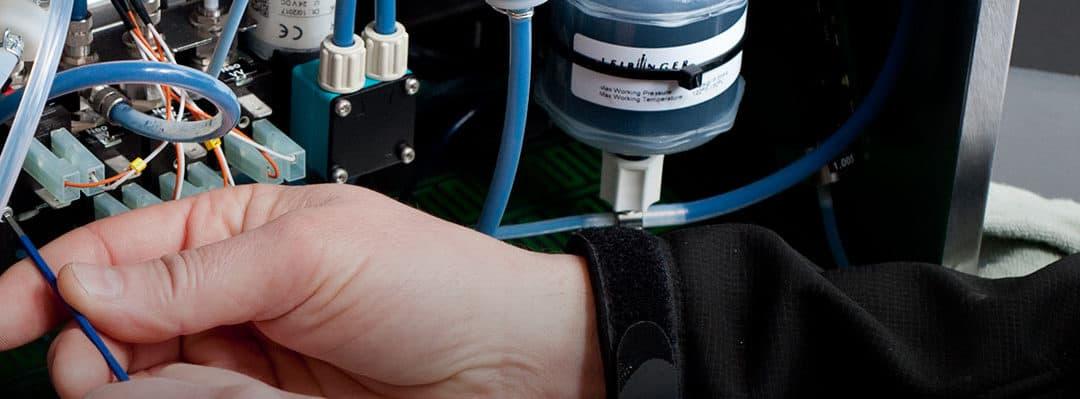
New Equipment Installation and Training
When you purchase equipment from Summit Packaging, we don’t just drop off a machine with a user’s manual and a “good luck.” Instead, our local service technicians come to your warehouse to properly install it. While we’re at it, we offer hands-on training tailored to your operations and maintenance teams.
For your operators, we go over everything you need to know to set up, turn on, and operate the equipment. This includes aligning your packaging and equipment needs, discussing common issues you may face, and offering tips for getting the most from your investment.
When we meet with your maintenance team, we go into deep technical detail. This includes the mechanical, electrical, and pneumatic elements of the systems, the unique requirements of the equipment you purchased, troubleshooting tips, and other information vital to keeping the equipment running as efficiently as possible.
Preventative Maintenance Program
Scheduled, routine maintenance helps keep your operations running smoothly while decreasing emergencies that causes expensive, unexpected downtime. Although routine maintenance does require some planned downtime, it’s on your terms and your schedule. Working together, we’ll determine the appropriate maintenance schedule for your equipment and your team. You can’t prevent parts from wearing out, but you can better prepare for when it happens.
During our preventative maintenance visits, our local technicians replace wear parts, adjust and realign machines as needed, verify that factory specs are being met, and complete other tasks necessary to the long-term life of your equipment. We also make recommendations based on your situation such as average run time, the type of packaging you use for the type of product you have, and more. For example, a machine being used in a wet environment, such as fish processing, needs different care than machines being used in a dry medical clean room.
Emergency Service
As we all know, despite the best preventative maintenance efforts, things happen. All parts have a life span, and even regular care and attention can’t stop parts from wearing out or prevent accidental damage to a machine during normal use. It’s difficult to know when it will happen, and there’s never a good time for it.
So, you’re in the middle of production when something goes wrong with your packaging equipment. What do you do? When you work with Summit, your first step is to call us, and we spring into action. Our technicians have been trained by our manufacturers, so we’re equipped to perform authorized factory service, whether you need a replacement part or high-level troubleshooting.
Since we’re local, our technicians can get to you quickly. There’s no waiting for an out-of-town rep to arrive while your production and shipping are stalled. Instead, we have staff dedicated to responding to emergency calls that come by phone, email, or our live chat tool. Along with efficient dispatching of our service technicians, we carry a large variety of parts locally in our warehouse, so in most cases we’ll arrive with the necessary parts rather than having to order them.
Training Classes and Support
In addition to the training you receive when you purchase equipment from us, we offer classes at your warehouse or office. We bring in our service experts, often joined by a manufacturer’s representative, and put on half-day or full-day clinics. The first part includes gathering in a conference room to cover the relationship between equipment and materials, the best material for your machines, ways to run as efficiently as possible, and other important issues. This holistic approach helps you better understand your equipment and materials.
After the classroom portion, we head to the production floor to give your team hands-on training with the equipment. At this point, we separate into two groups — operators and maintenance teams — for specialized training. This dramatically increases your understanding of your machines and boosts self-sufficiency. It also gives everyone a chance to ask questions, pick up useful tips, and learn more about the equipment.
Taken together, these four pillars of maintenance help you boost productivity and reduce unexpected downtime. To learn more about our approach to service and preventative maintenance, please contact the Summit customer service team.