Automation offers a way to bridge the staffing gap, enabling continuous production and reduced operational costs. Selecting the right automation technology requires careful evaluation of its integration with existing systems and its scalability. Effective adoption involves not only technological upgrades but also involving team members early in the planning process to tailor the automation effectively. This strategic approach guarantees that automated systems not only fill staffing voids but also improve overall efficiency and operational flow. Further insights reveal the deeper impacts of these integrations.
Article Main Points
- Automation equipment increases production by operating continuously, filling staffing gaps.
- Robotic devices ensure precision and quality, enhancing product consistency.
- Mechanization reduces production costs by minimizing halts and operational errors.
- Proper integration of automation with existing processes prevents operational congestion.
- Detailed planning and specialist consultation ensure successful automation implementation.
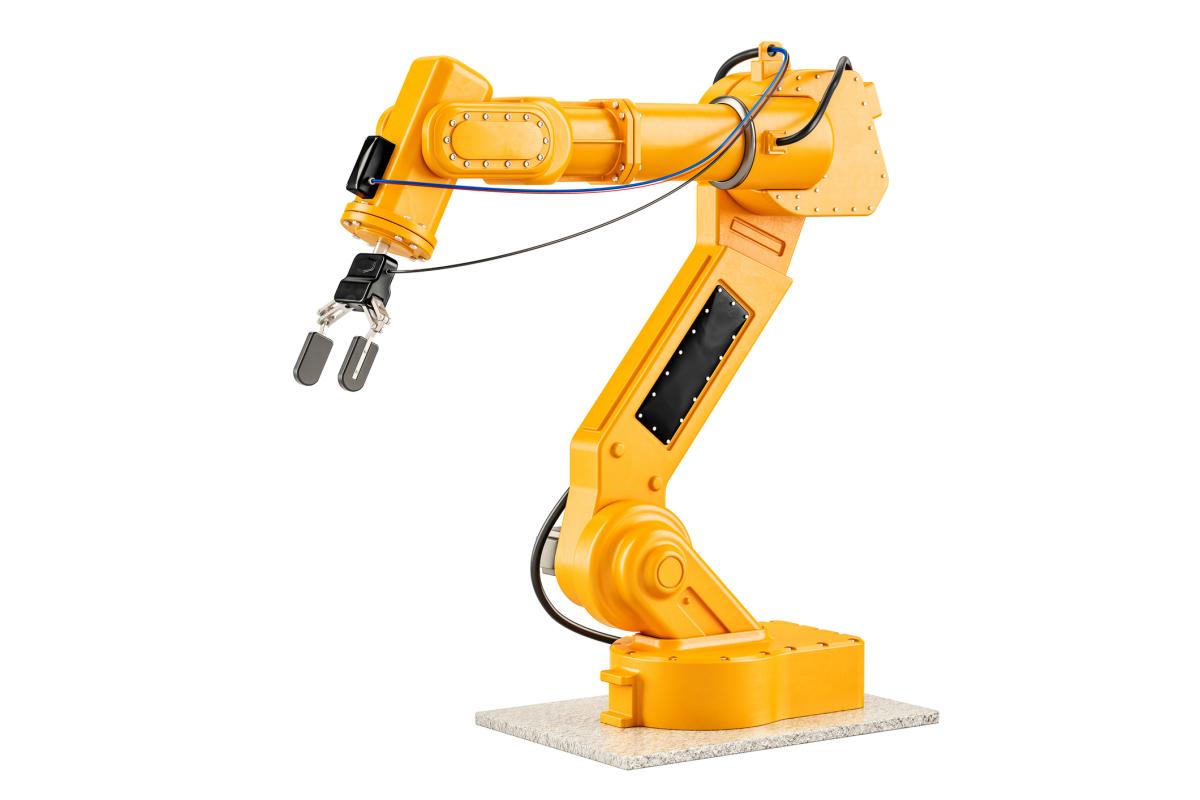
Automation Solves Labor Shortage
Yes, automation addresses the labor shortage effectively.
In the realm of production, automation serves as a strategic remedy. It reshapes the needs for human workers in factories. As companies face challenges in hiring sufficient staff, the adoption of mechanization tools bridges this gap and drives companies towards improved output and greater efficacy. This change proves essential in today's market with its high demands for prompt, reliable, and economical product delivery.
In these processes, robotic devices and AI-guided apparatus are crucial. They execute operations with heightened precision, reducing errors commonly seen with manual labor. Such accuracy is vital for sustaining product quality and uniformity, which in turn strengthens company reputation and consumer trust.
Furthermore, these mechanized systems excel at reducing production halts. Their capacity to function continuously without pauses for rest or changes in shifts leads to non-stop production flows, enhancing production volumes significantly. This continual activity is instrumental in achieving cost reductions, as it maximizes resource and power utilization, thereby lowering total production costs.
Finding the Right Fit
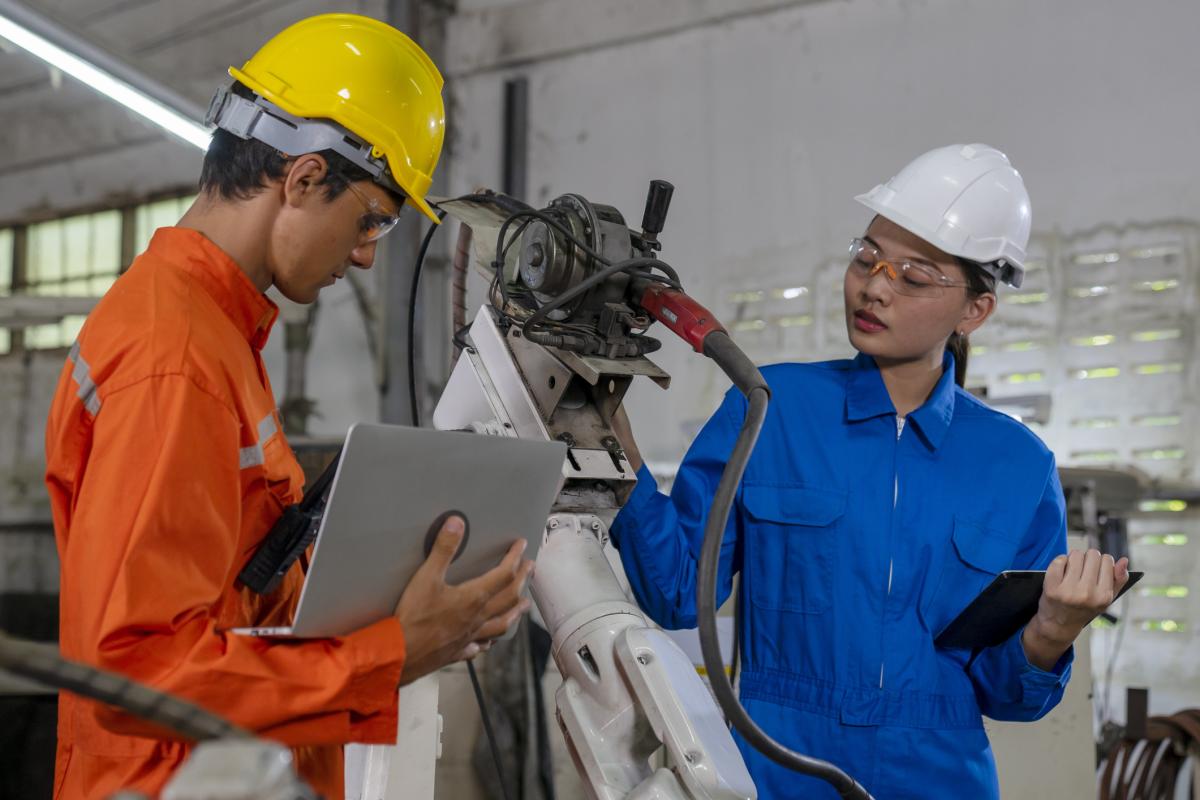
To effectively handle labor shortages, selecting the right automation technology is essential. This decision demands a strategic approach: each device or software must fit the existing procedures and boost team productivity. Mistakes in this choice can cause workflow inefficiencies or unnecessary extra training for staff, undermining the desired efficiency improvements.
Automation is not a one-size-fits-all solution. Some companies, unfortunately, fall into the trap of simply buying equipment because they think "all automation is good." A company must examine the specific functions the automation will serve and how it integrates with current operations. This understanding ensures the automation enhances rather than disrupts the production process. The company needs to evaluate if the automation can scale and handle the company's complexity.
Involving team members in the early stages of planning can pinpoint training needs in advance. This forethought not only facilitates a smoother transition but also utilizes staff insights for more effective technology integration, boosting the firm's operational capacity and efficiency.
A Cautionary Tale
A poorly planned automation investment can fail dramatically. One local business we know recently purchased a robotic palletizer without considering how it would affect the flow of materials upstream. This resulted in a bottleneck at an earlier stage in their production line, negating some of the potential benefits of the palletizer.
This example highlights the necessity of meticulous planning in equipment integration. Proper automation should improve, not hinder, existing procedures. To avoid such errors, a comprehensive understanding of how new machinery will interact with existing setups is crucial. Enterprises considering automation must undertake thorough assessments and perhaps seek advice from specialists to ensure that all components of the manufacturing process are in sync, thus genuinely boosting productivity and effectiveness.
A Success Story
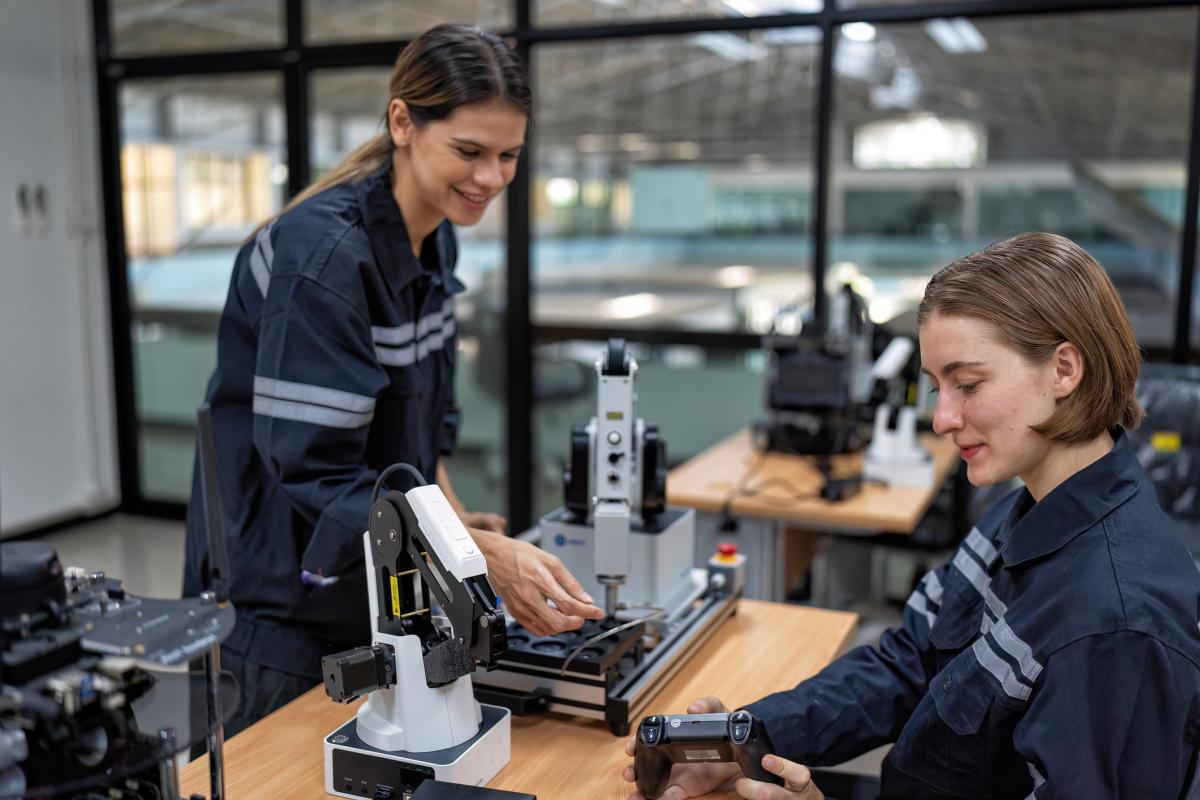
Partnering with a team of engineers and technicians from the start can lead to successful automation integration. In a story of success, a client's early collaboration with Summit Packaging demonstrated successful automation integration. We took the time to understand their specific challenges, product flow, and production goals. Through careful analysis, we identified several key areas where automation could significantly improve their efficiency. We then recommended a combination of equipment, including robotic case packing and automated labeling systems. These systems seamlessly integrated with their existing infrastructure. The result? A significant increase in production output with minimal disruption to their workflow.
Furthermore, this shift led to improved operational flow, benefiting and uplifting the current workforce. Employees moved from repetitive duties to more meaningful roles, improving morale and involvement. This strategic adoption of automation laid a strong groundwork for continuing productivity growth, aligning with the client's ongoing strategic objectives.
The Benefits Go Beyond Labor
Automation extends benefits beyond merely addressing the labor deficit. Firstly, this technological integration enhances productivity. Devices operate tirelessly, ensuring both high output and consistent quality across products.
- Reduced Overhead Costs: Automation can significantly reduce labor costs, which can have a positive impact on your overall production budget.
- Improved Safety: Repetitive tasks that can lead to workplace injuries can be automated, creating a safer work environment for your employees.
- Increased Consistency: Automated systems can operate with greater precision and consistency than manual labor, leading to a higher quality product.
- Improved Efficiency: By automating tasks, you can streamline your production process and increase your overall output.
Don't Let Fear Hold You Back
No, fears of job displacement should not deter your company from implementing automation technologies. These tools enhance productivity and spark creativity, making them essential in today's fast-paced business environment.
Automation fills labor shortages and encourages strategic tech investments, securing long-term business achievements. It boosts efficiency, crucial for handling increased production needs without sacrificing quality. Furthermore, it shifts skilled resources from repetitive tasks to more intellectually demanding roles, elevating employee skills and job satisfaction.
Additionally, workforce empowerment results as staff adapt to new technologies. This enhances their organizational value and equips them with skills for the future. View automation not as a human replacement but as a complementary force that boosts workforce capabilities.
Therefore, balance job displacement concerns with automation's benefits like creating more stimulating, less strenuous jobs. See automation as a collaborator to unlock maximum potential and achieve sustainable growth in a competitive market.
The Future of Work
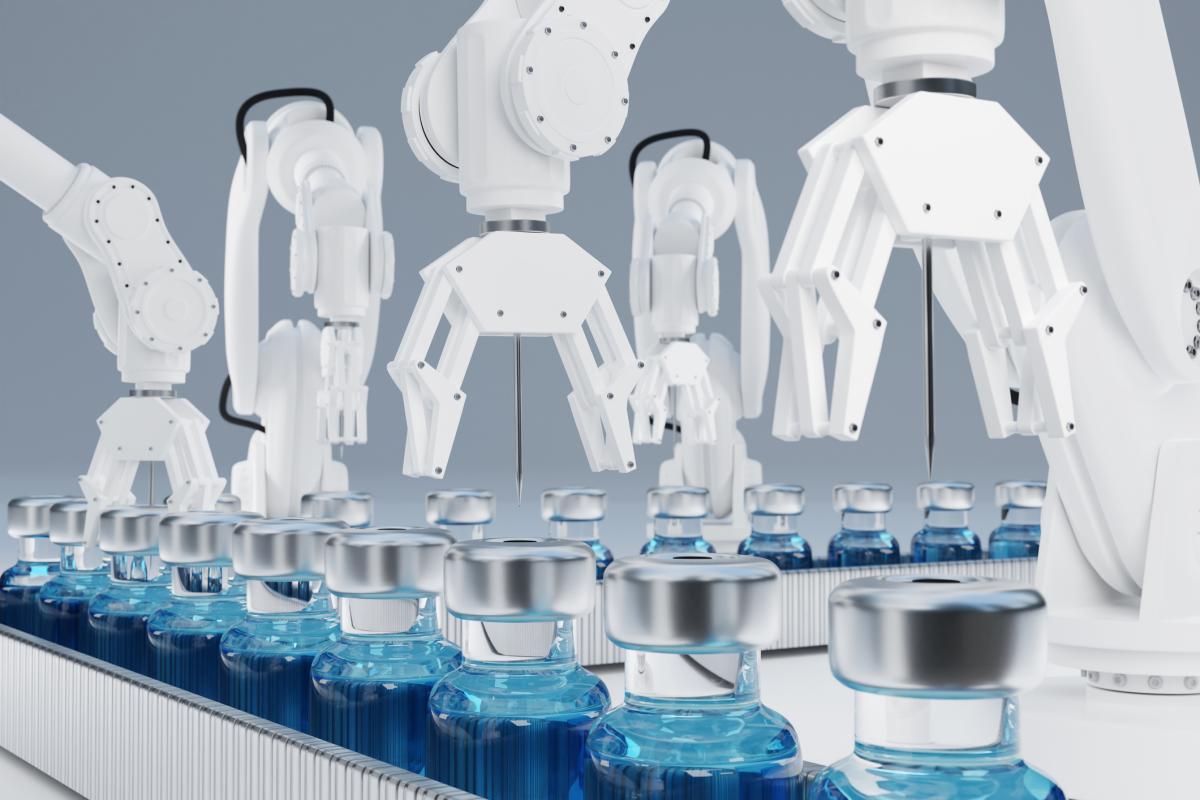
The future of work, particularly reshaped by automation, offers progressive companies a chance to lead in a shifting marketplace. As technological advancements quicken, they spark extensive changes in the workforce, setting a scene where being adaptable and visionary is crucial.
In the next article, we'll delve into Summit Packaging's unique approach to helping businesses leverage automation to achieve their production goals. We'll explore our proven methodology, showcase our expertise, and demonstrate how we can be your partner in navigating the successful implementation of automation solutions.